At semiconductor fabrication plants and foundries across the world, Emerson’s level Instruments have gained their reputation and trust to deliver accurate and reliable level measurement. The technologies required in the semiconductor industry are some of the most dynamic, sophisticated, and competitive. As the industry continues to grow, so does the demand for ultra-pure gases, wet chemicals, dry solids, and bulk storage, raw materials to semiconductor manufacturing.
Fab operators need a reliable and responsive equipment suppliers and instrument providers with a global reach and technical capability to ensure the highest quality, manage costs, reduce environmental impact, and innovate for the future. Emerson level instruments help semiconductor chip producers to increase throughput and stay competitive in high-growth markets without compromising the safety and maintenance in the applications that rely on precise level measurement in tanks that contain hazardous and harsh media.
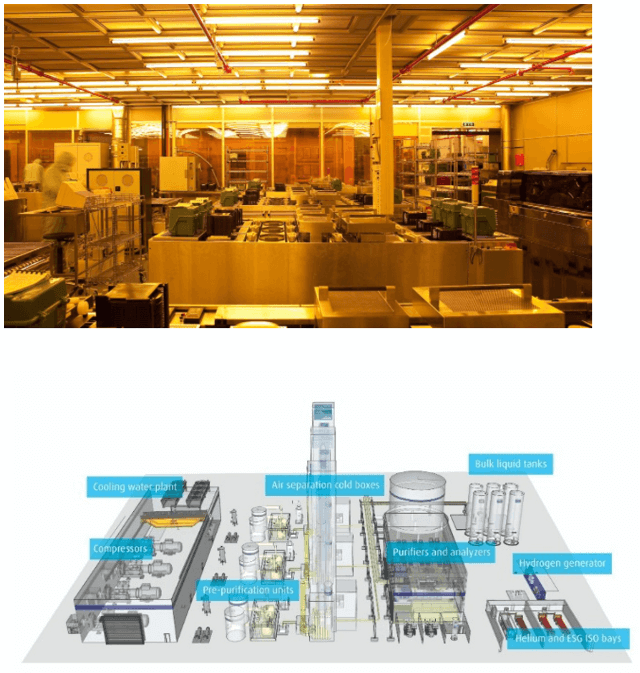
Figure 1 (top): A view of the inside of semiconductor fabrication facility; Figure 2 (bottom): Onsite bulk liquid, chemical and gas storage to semiconductor fabs
In this post, we will discuss two specific case studies where Rosemount Level instruments have solved technical challenges posed to the semiconductor customers.
Case Study 1: Semiconductor Manufacturer Reduces Safety Risk and Production Lost with Rosemount 3300 Guided Wave Radar Level
A customer in North America was looking for the perfect level solution to read accurate level measurement from tanks containing corrosive fluids with condensing vapors in the offsite utility processes including scrubbing, neutralization, and disposal of acid waste streams.
A neutralization system reduces the acidity used in semiconductor manufacturing prior to disposal. The semiconductor manufacturer was not able to measure liquid level accurately and reliably in their day tank, acid receiving, acid neutralization and brine storage tanks. Competitive ultrasonic level transmitters were installed on the OEM (original equipment manufacturer) supplied neutralization system. The variance in level measurement was as high as 70% erroneous during startup due to condensation buildup on the sensor of the ultrasonic transmitters.
To obtain usable readings, operators would knock on the side of the tank to dislodge condensation from the transmitter and to determine the approximate tank level by audible sound manually. Due to measurement variability and high liquid level, the acid neutralization system would often shutdown. The process had to be operated manually to recover from high-level trips.
There were three significant negative business consequences. The first was a risk to personnel safety as the tanks were inside a building. In the event of a tank overflow, operators could be exposed to acid. Second, there is a risk of environmental contamination and cleanup costs if an acid spill occurs. Third, there was a safety risk associated with operators needing to knock on the tanks to try to get a level reading. Finally, if a tank is too full to accommodate a batch of acid, it will stop production. It will take 2 to 6 hours to recover and results in loss of production time which translates to permanent revenue loss.
To resolve the problem, the manufacturer installed Rosemount 3300 Guided Wave Radar level transmitters on all the tanks in the acid neutralization process stream. Operators no longer need to knock on the side of the tanks to obtain level readings or estimates. The process is reinstated to automatic control and there is no more lost production.

Figure 3 (left): Offsite Utility Site of the customer; Figure 4 (right): Rosemount’s Guided Wave Radars – 3300 series & Superior Performance 5300 series
Case Study 2: Semiconductor Manufacturer Solves Level Reliability with Rosemount 5408 Non-Contacting Radar on Tanks Containing Harsh Chemicals
The semiconductor customer has several storage tanks onsite with a proprietary liquid chemical mixture. The chemicals are corrosive, toxic and vapors formed on some of the tanks. The chemicals are predominantly acids, alkalis, and other chemical solvents used for etching and cleaning of silicon wafers. To measure liquid levels in each tank, they used either displacer floats and manual testing such as dip and tape, or just a visual inspection of the tank level.
The process temperature of the liquid chemicals is at 122 °F (50 °C), stored in a tank that’s 6.5 ft. (2 meters) tall. None of these manual testing methods are safe for the operator to measure the level, nor are they accurate. The customer needed a safer and more reliable way to measure tank levels.
The customer selected Rosemount 5408 Non-Contacting Radar level transmitter and process seal antenna as they are reliable and resist corrosion. The Rosemount 5408 uses the principle of frequency modulation continuous wave technology (FMCW), which maximizes the strength of the radar signal to obtains a robust measurement value. Through the internal EMC design and surge isolation, noise-free output can be achieved, and the unique radar wave path protects the signal from external interference. The measurement will not be affected by factors such as medium density, temperature, and pressure.
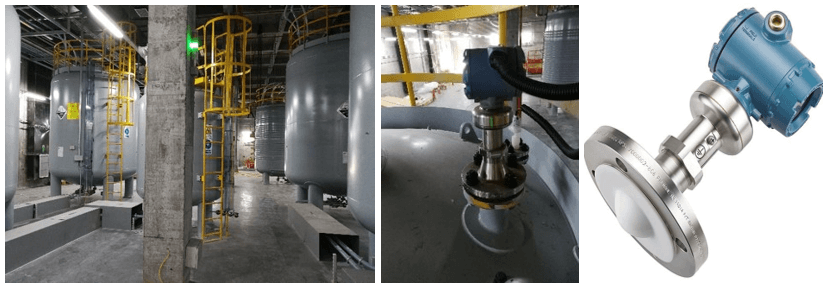
Figure 5 (left): Chemical storage mezzanine level of the customer; Figure 6 (center): Rosemount Non-Contacting Radar installed on the Chemical Storage Tank; Figure 7 (right): Rosemount 5408 Level Transmitter with Process Seal
After trialing a Rosemount 5408 level transmitter and seeing the success, the customer purchased and installed another 40 radar devices: one for each of the 40 tanks at the plant that contained different chemicals with their own pressure and temperature conditions. Here are some key benefits:
- Reduced man hours as manual measurement is no longer needed
- Improved safety
-
Accurate measurement management
“Without the need for manual level testing, safety was greatly improved.” – Plant Supervisor
Conclusion
Bulk gases and wet chemicals comprise a significant portion of supply spend for semiconductor and display fabs. Effective supply often requires on-site production, storage, and distribution. These facilities are built concurrently with the fab to ensure wet chemical, liquid and gas deliveries are made available as soon as the fab is operational.
Emerson’s complete level instrument portfolio that comprises of process level, cryogenic capabilities with level measurements spanning liquid and gas measurements can be applied to any of the possible issues faced on the liquid and gas tanks in semiconductor fabrication facilities.