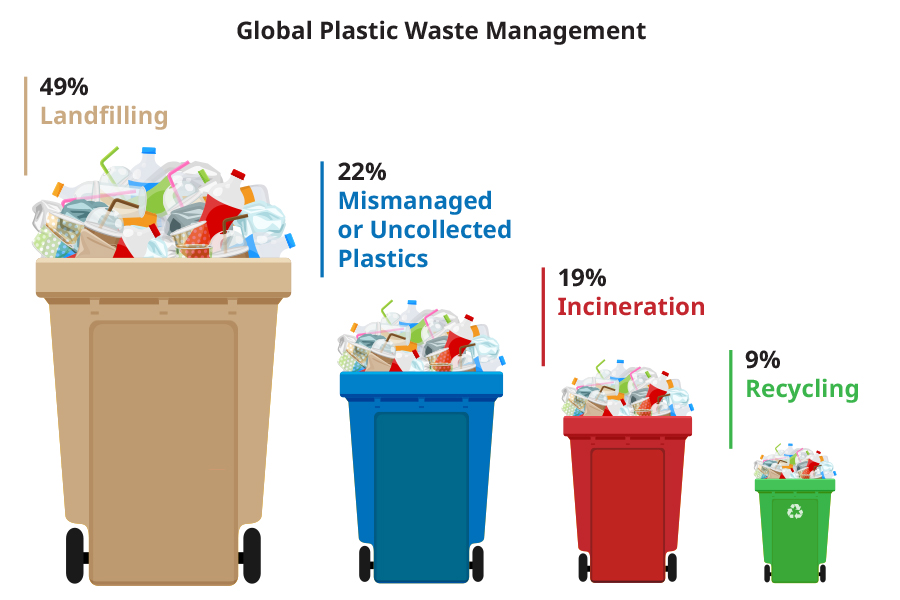
Global plastic waste by waste management category. More than 90% of plastic is never recycled. Source: OECD Global Plastics Outlook (2022).
Only about 9% of the world’s plastic waste is recycled, according to the Organisation for Economic Co-operation and Development (OECD). Many post-consumer plastics are considered unrecyclable via traditional mechanical methods and end up in landfills, get incinerated, or pollute the environment. Mechanical recycling is limited to remelting plastic waste, sorted by color and material, which is challenging because there are at least three major plastic groups commonly in use. This recycling method is not suitable for every kind of plastic because some polymers lose quality during remelting,—and PETE, HDPE, and PP have different melting points and may not mix in liquid form.
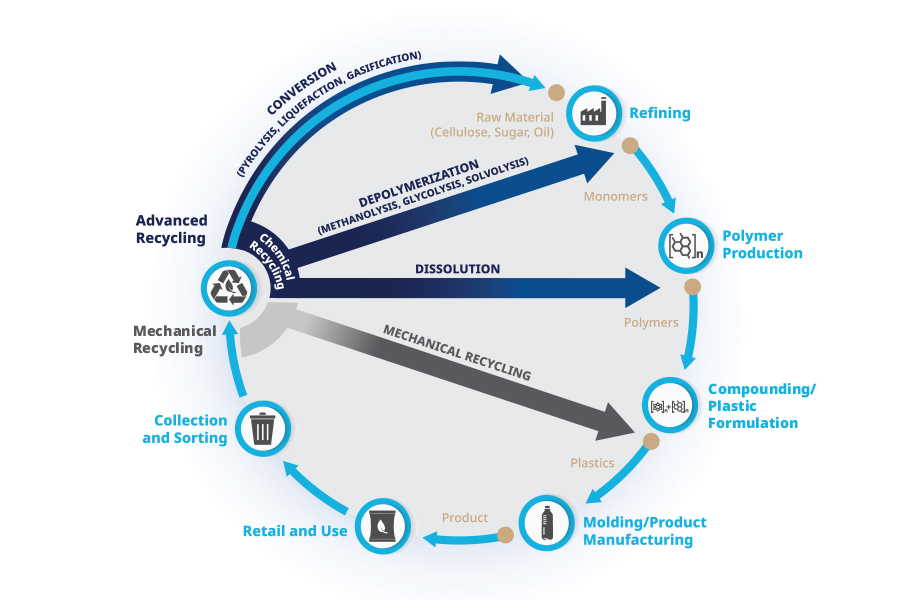
The complete plastic production chain begins with new plastic from scratch, including every step of the process. Plastic recycling is part of the chain. Chemical and mechanical recycling can work together to address different waste streams.
Advanced recycling, a collection of emerging chemical recycling technologies, offers a potential solution to increasing the recycling rate by turning plastic waste back into its molecular building blocks, becoming the raw material for making new plastics, transportation fuels, and other products. There are different chemical recycling technologies, including conversion, depolymerization and dissolution.
In an article published in Plastics Machinery & Manufacturing magazine, I cover plastic waste recycling via conversion. Conversion returns plastic refuse to the source molecules via pyrolysis and can handle minimally sorted waste.
Pyrolysis works with mixed or minimally sorted waste, including the three most common varieties: PET, PP, and HDPE. When waste is heated without oxygen in a pyrolysis reactor, solid mixed plastics can be gasified and liquified. The heat applied may be dry, or it can be injected as water and supercritical steam.
Selection of heating method depends on the desired result.
Dry heat breaks down the plastic completely, turning it entirely into syngas, which is a mix of hydrogen and carbon monoxide. Using water and steam allows mixed plastics to be heated to critical temperatures in the presence of a catalyst, breaking down the polymeric bonds to yield short-chain, stable hydrocarbons. With distillation as a separation step, fractions can include combustible gases, various-weight hydrocarbons and even carbon solids.
The common element to both is heat, requiring an energy source. This usually involves a fired heater and/or a boiler where steam is necessary. The article examines several possibilities, but we’ll focus here on fired heaters and how to control three main process variables—flow, temperature, and pressure—each applied primarily to process fluid, and especially fuel. A fully outfitted fired heater, as is necessary to optimize production, depends on a variety of instruments. There are several possibilities for process fluid feed flow measurements:
- Rosemount™ 8800 Single or Quad Vortex Flow Meter
- Rosemount™ 9295 Process Flow Meter
- Micro Motion™ ELITE™ Coriolis Flow Meter
- Rosemount™ 3051SFA Annubar Flow Meter
- Flexim FLUXUS® F721 Non-Intrusive Liquid Flow Meter.
Why you would pick one over another depends on the application specifics, and our application engineers can help with the selection process.
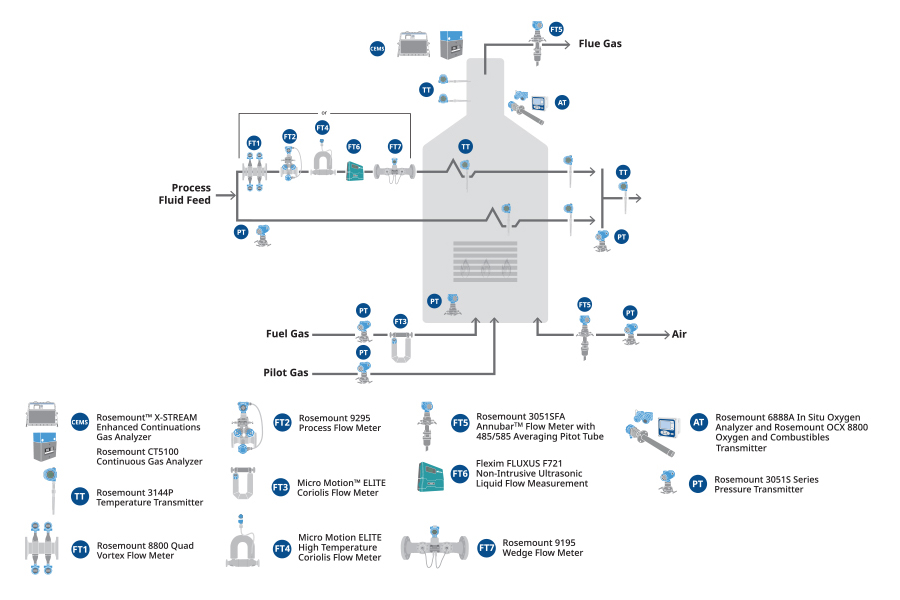
Maintaining control and optimizing fired heater performance depends on data and actionable insights from strategic instrumentation.
For fuel flow, Coriolis technology is ideal because Coriolis flow meters can measure density as well as mass flow, giving them the ability to compensate for varying energy content of fuel gases. The article also looks at optimizing steam generation and consumption, corrosion monitoring, safety strategies, and more.
Solving plastic waste is a global challenge but with innovation, collaboration, and policy engagement, closing the circularity gap and driving real change is possible. For advanced plastics recycling processes, automation is a key strategic lever to scale up production and maximize operational efficiency.
Partnering with a supplier able to provide a complete portfolio of automation solutions, together with extensive domain expertise, can help to reduce project complexity and drive operational efficiency, while maximizing plant safety and reliability. Emerson’s automation technologies are designed to optimize plastic recycling units by delivering precise control, increased process visibility and actionable information for improved decision-making.
Read the article for more information on how automation and data from intelligent measurement instrumentation help optimize operational performance in circular plastics facilities.