When it comes to measuring flow, you have many choices among technologies. For gas, liquid, and steam flow metering applications, vortex technology is an option.
If you’re unfamiliar with how Vortex flow meters work, Wikipedia describes it:
Another method of flow measurement involves placing a bluff body (called a shedder bar) in the path of the fluid. As the fluid passes this bar, disturbances in the flow called vortices are created. The vortices trail behind the cylinder, alternatively from each side of the bluff body. This vortex trail is called the Von Kármán vortex street after von Kármán’s 1912 mathematical description of the phenomenon. The frequency at which these vortices alternate sides is essentially proportional to the flow rate of the fluid. Inside, atop, or downstream of the shedder bar is a sensor for measuring the frequency of the vortex shedding. This sensor is often a piezoelectric crystal, which produces a small, but measurable, voltage pulse every time a vortex is created. Since the frequency of such a voltage pulse is also proportional to the fluid velocity, a volumetric flow rate is calculated using the cross sectional area of the flow meter. The frequency is measured and the flow rate is calculated by the flowmeter electronics using the equation f=SV/L where f is the frequency of the vortices, L the characteristic length of the bluff body, V is the velocity of the flow over the bluff body, and S is the Strouhal number, which is essentially a constant for a given body shape within its operating limits.
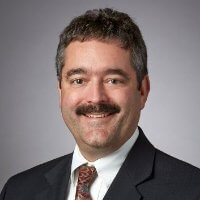
Robert Zaun
Marketing Director
He opens highlighted some of the strengths in vortex flow measurement technology such as no moving parts, excellent rangeability (“the ratio of the maximum full scale range to the minimum full scale range of the flowmeter”) and a 30-to-1 turndown ratio.
https://www.youtube.com/watch?v=Hlbz3qxkqd0
To address noise at low flow rates, Robert describes adaptive digital signal processing (ADSP) to help extend the rangeability of the meters and along with using a mass-balanced sensor, minimize the impact of vibration in the process.
He also highlighted the flow simulation capability which simulates the vortex signal coming from the process to verify correct operation of the transmitter. This provides in-situ verification which means the meter does not have to be removed from the line to verify that the electronics in the transmitter are working properly.
You can connect and interact with other flow measurement peers in the Flow track of the Emerson Exchange 365 community.