If you’re responsible for reliability in your process manufacturing or production operations, you may have seen the ARC Advisory Group’s report, Proactive Asset Management with IIoT and Analytics.
I’ll highlight a few points from the article and from reliability experts around Emerson Process Management. The article opens:
The Industrial Internet of Things (IIoT) with advanced analytics, offers new opportunities to improve the reliability of industrial assets, enabling owner-operators to progress toward no unplanned downtime, which many consider to be the ultimate objective for maintenance and operations.
Preventive maintenance assumes a failure pattern that increases with age or use. Unfortunately, this applies to only 18 percent of assets. The other 82 percent of assets display a random failure pattern. In contrast, predictive maintenance (PdM) approaches employ condition monitoring data to predict failure. Proactive maintenance goes further by combining multiple variables with analytics to predict failure with a higher degree of confidence and fewer false positives.
Here’s the detail on this 18% statistic:
…data on failure patterns compiled by NASA and the US Navy (see chart on page 3) show that only 18 percent of failures are age related, and 82 percent have a random pattern. Based on these data, preventive maintenance (PM) provides a benefit for just 18 percent of assets. Doing a PM on the other 82 percent may well cause failures by placing the asset at the beginning of the Type B curve for early life failures.
Condition monitoring is used in predictive maintenance:
…to provide advanced notice of a failure so appropriate maintenance can be scheduled and performed to prevent the unplanned downtime.
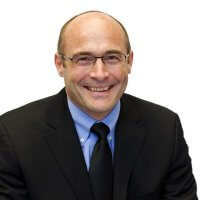
Will Goetz
Vice President
Reliability Consulting
Unfortunately, the time-based task backlogs in most companies’ systems often prevent them from realizing any significant business performance improvement from predictive software or special purpose integrations.
Will’s experience in speaking with manufacturers and producers is that only when predictive is aligned to the system where work is managed will the business benefits from increased availability and lower maintenance costs be realized. The key is to focus on improving the EAM data and ensure that their workflows are aligned to inputs from advanced predictive capabilities.
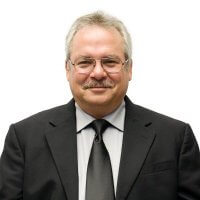
Bruce Hawkins
Director of Technical Excellence
At worst, we have destroyed the organization’s faith in the technology, which in turn increases resistance to its future implementation. Operations will be more reluctant to release equipment to Maintenance because, “you’re using those fancy tools, but it breaks anyway”.
Pervasive Sensing technologies are making it possible to collect data to support condition monitoring and advanced analytics. These analytics are providing reliability professionals new ways to analyze the data, including search, contextualization, and pattern recognition.
One major concern is that expertise to make sense of the data, manage the analytical models, and to interpret the results is increasingly in short supply. One way this scarcity of expertise is being addressed is through remote monitoring as part of an Integrated Operations (iOps) program. These programs are becoming more common for companies to gain insights from data by leveraging expertise wherever it exists and allowing these experts to support global operations.
You can connect and interact with other reliability and maintenance experts in the Reliability & Maintenance group in the Emerson Exchange 365 community.