Even non-critical pumps in your process can cause spills, vapor clouds, fires and worse. Most of these failure incidents provide warning well in time to solve the problem—if feedback mechanisms are in place for your operators and maintenance personnel.
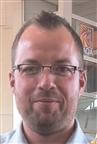
Cranford Johnstone
Sales Manager – Reliability Solutions

He opens:
PETROCHEMICAL plants have a large number of pumps that are continually in use for functions that range from feedstock supply to product distribution. Pump repairs typically consume up to 7% of the total maintenance budget and therefore must be carefully considered within an overall maintenance programme.
He notes that typically less than 5% of the pumps—the most critical ones—are typically continuously monitored with machinery protection systems. And, of the conditions that can lead to pump failure, according to author Ron Moore:
…up to half of all failures are process induced and are therefore preventable.
Conditions causing pump failure include process operating conditions and mechanical wear. Cranford gives an operating condition example:
…when changes in operating conditions induce pump cavitation (a result of insufficient net positive suction head), this can grossly accelerate impeller wear and lead to seal failure.
Mechanical wear can manifest itself in several ways:
…imbalance, poor shaft alignment, loose pump mounts, broken bolts, foundation cracks, and damaged impellers. These defects gradually decrease the integrity of the machine and can lead to coupling, seal and bearing failures.
The traditional approach to inspecting the majority of pumps without online condition monitoring systems has been:
…by monitoring vibration, commonly by manual measurements on a periodic basis – typically every 30–90 days. Assuming that a trained analyst is available to review the data, these periodic checks can be used to detect many faults in advance; even then, however, they still leave the plant vulnerable to unplanned outages in between measurements.
What’s missing is real-time feedback with a clear indication of pumps in distress and the severity level of the fault. Cranford a way this feedback can be provided through monitoring raw vibration and high frequency impact faults. I highlighted the PeakVue Analysis diagnostics for these impact faults in a post, The Peaks Provide the Early Warning in Machinery Protection.
He describes how wireless technology has made collecting vibration and other data to gauge pump health more feasible:For example, for a total picture of pump health we also need pressure monitoring to check for clogged suction strainers as well as pre-cavitation. If these values are not already being monitored, wireless pressure transmitters can be added easily and affordably.
Readings for vibration, impacting and pressure can all be broadcast over the same wireless network, and the system can be easily expanded to include temperature, level, flow and many other parameters. Users can monitor online for the conditions that are of greatest concern, including cavitation, bearing temperature, vibration, process leakage, suction strainer differential pressure, discharge pressure, seal reservoir level and pressure.
By providing early warning to failing pump health, safety, environmental, and production-related incidents can be avoided. Read the article for more on common threats to pump health, paying attention to the role of control valves, and how these technologies have been applied at the SABIC olefins plant in Teesside, UK.
You can also connect and interact with other reliability experts in the Reliability and Maintenance group in the Emerson Exchange 365 community.