So how exactly does Formula 1 (F1) racing compare with process manufacturing and production?
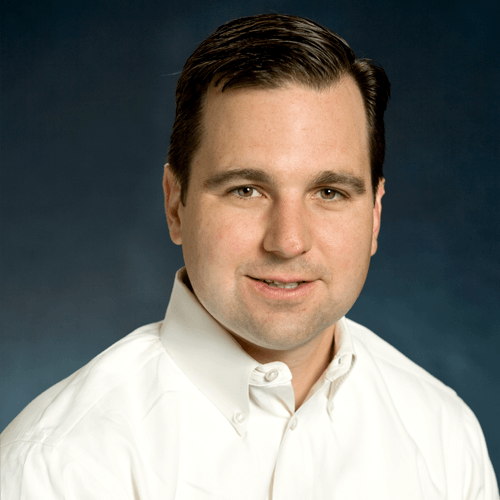
Mike Boudreaux
Director, Remote Asset Monitoring and Analytics
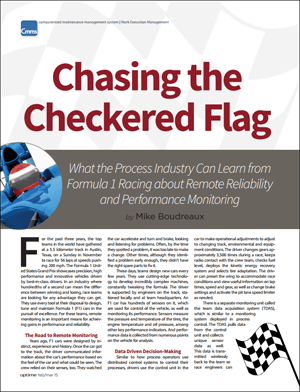
Key to this success is the focus on reliability and performance monitoring from remote experts. Mike opens noting how F1 racing was done years ago:
F1 cars were designed by instinct, experience and history. Once the car got to the track, the driver communicated information about the car’s performance based on the feel of the car and what could be seen. The crew relied on their senses, too. They watched the car accelerate and turn and brake, looking and listening for problems. Often, by the time they spotted a problem, it was too late to make a change. Other times, although they identified a problem early enough, they didn’t have the right spare parts to fix it.
But technology has significantly changed how F1 crews operate:
…teams design new cars every few years. They use cutting-edge technology to develop incredibly complex machines, constantly tweaking the formula. The driver is supported by engineers on the track, stationed locally and at team headquarters. An F1 car has hundreds of sensors on it, which are used for control of the vehicle, as well as monitoring its performance. Sensors measure the pressure and temperature of the tires, the engine temperature and oil pressure, among other key performance indicators. And performance data is collected from numerous points on the vehicle for analysis.
With this data, it’s:
…transmitted wirelessly back to the team so race engineers can perform remote analysis to enable better and faster decisions about how they set up and configure the car.
And this data is not just for the pit crew at the track, it’s:
…also sent wirelessly via satellite to the team’s headquarters where additional computers store the data for use in simulations, trending and future design. Before any changes are made to the car on the track, the team will run the simulation multiple times at headquarters to ensure they’re making the right decision.
So how is this like our process industries?
A wide variety of technology enablers currently available have made adoption of integrated operations increasingly common. New sensor technologies are available that are less intrusive and more cost-effective, including corrosion, ultrasonic, acoustic and infrared. Wireless technologies, such as WirelessHART and 4G networks, have enabled easier collection of data. Access to and reliability of the Internet have become ubiquitous. Collaboration tools, such as video conferencing and social media, make it easier to make informed decisions, no matter where members of the team are located. Advances in display technologies and high fidelity process simulation have made virtual training a reality. The increase in the ability of devices to communicate about themselves, the ability of pervasive sensing to capture a whole new level of site operations data and the use of big data for analytics promise even better monitoring for increased reliability.
Remote monitoring connects additional data with experts to improve reliability and performance:
…in process automation assets, as well as production assets, is increasing. End users are monitoring the condition of critical assets, such as turbines, blowers, cooling towers and heat exchangers. They are also remotely monitoring control systems, instrumentation and valves. And new sensing technologies are enabling remote monitoring of site safety, energy use and the environment.
These experts may be employees or third-party process and reliability experts depending on the scale of the process manufacturer or producer. Just like the F1 teams, this collaboration leads to improved performance.
Mike concludes:
The stakes and the payoff in reliability and performance improvements for implementing remote monitoring capability in the process industry are even greater. Some process companies may see remote monitoring capabilities as a vision for the future. But the fact is, the future is here for the process industry. The technology and expertise exist today and adoption is gaining momentum.
Read the article for more on ways to bring these technologies, expertise and collaborative communications in raising your performance level.
You can also connect and interact with other reliability and process improvement experts in the Reliability & Maintenance and Improve & Modernize in the Emerson Exchange 365 community.