If you have an instrumentation and automation project for a new installation you are faced with many technology selection decisions.
For instance, instrumentation based on digital communications technologies, which provide robust diagnostics and predictive capabilities such as Foundation fieldbus, have been with us for nearly two decades. And wireless instrumentation, built on standards such as WirelessHART (IEC 62591 – 2010) and ISA-100 (IEC 62734 – 2014) are being put to use.
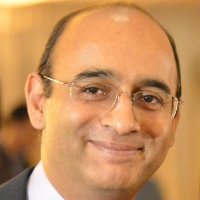
Moazzam Shamsi
Global Solutions Architect
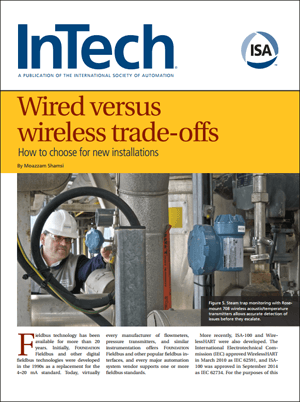
When analyzing the use of wired or wireless instrumentation for existing plants, Moazzam notes that the existing infrastructure is factored in and:
…the choice hinges on a straight comparison of the two technologies and the application of the solution that makes sense.
Without the infrastructure, this cost of installation must be considered.
For wired devices, the Foundation fieldbus standard provides:
In practice, 12 to 16 instruments are typically installed on a fieldbus segment.
Concerning the length of the segment:
Typically, up to 12 devices can be installed on a fieldbus segment up to 120 m long. If the process unity has more than 12 instruments, a second or third segment can be installed.
To avoid problems on a segment such as short circuit:
…many plants install a segment protector or device coupler, allowing multiple instruments to connect at one location. The device coupler is installed in an enclosure near the process unity. Connections to the individual instruments are called spurs.
The segment includes a fieldbus power supply to power the devices on the segment and an H1 card connecting the segment to the distributed control system. The fieldbus power supply and H1 card are integrated in some systems. Moazzam notes that segments can be redundant for critical process units and made intrinsically safe with barriers for hazardous locations.
He offers guidance for where to use fieldbus:
…a process unit containing many flow, pressure, temperature, level, multivariable, and other instruments, all within a reasonable distance of one another.
Segment design tools simplify segment planning. Moazzam shares that for existing installations undertaking a modernization project:
…HART can use existing 4-20 mA wiring from older instruments to carry digital signal information to the device couplers. The device couplers can be installed in the old marshalling cabinet, saving a considerable amount in wiring and labor costs. Although HART does not have performance levels comparable to newer fieldbus technologies, it is the least costly wired digital option, and often sufficient from an operational standpoint.
Wireless devices:
…do not require communication wiring and related infrastructure…the vast majority use battery power and thus operate without wires. Wireless networks communicate data back to host systems securely and reliably, and can be applied to both control and monitoring applications.
He describes how wireless devices, networks, and gateways to the control systems operate. You can get some of this background in earlier posts, such as Designing Communications Reliability into the WirelessHART Standard and Tips and Tricks in Deploying Wireless Field Networks.
Moazzam highlights the advantages of wireless devices:
…they can be installed virtually anywhere in an efficient, timely, and cost-effective manner….require no wired infrastructure or local power supply, so they can be far away from a process unit’s wired fieldbus and power wiring.
He sums up the advantages of Foundation fieldbus and WirelessHART respectively:
Foundation fieldbus
- Widespread support among instrument suppliers
- Supported by almost every automation system supplier
- Familiar to maintenance personnel
- Excellent for control
- Decades of operating experience
- Best for multivariable instruments and multipoint devices
- Digital data shows raw measured signals
- Extensive diagnostics
- Less wiring than 4–20 mA
WirelessHART
- Significant reduction in installation complexity
- Inexpensive
- Reduces space, weight, and power requirements
- Easy to expand to accommodate changes and additions
- Excellent for monitoring applications
- Can be used for control in some circumstances
- Best for hard-to-reach locations
- No need to modify existing wired infrastructure
- Can reduce the need for fixed asset inspections, reference to IEC60079 Part 17
- Allows measurements to be made where fieldbus is not practical or feasible
Read the full article for examples of process manufacturers and producers achieving results with both technologies and more on the considerations on the right technologies to select for your project.
You can also connect and interact with other wireless and project experts in the Wireless and Plan & Design groups in the Emerson Exchange 365 community.