Whether it’s your car or an asset in your production facility, running it to failure can be costly, unsafe and inconvenient. In terms of maintenance reliability, the U.S. National Response center noted that “…it costs 50% more to repair a broken component than one that was addressed prior to its failure.” And that statistic does not consider the cost of lost production, overtime and other costs.
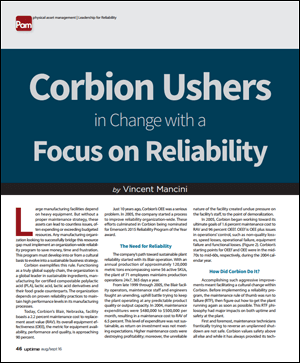
The article, written by a Corbion maintenance and reliability engineer shares the story of making a cultural change around reliability and achieving significant quantified business results.
Through their focused efforts, this facility:
…boasts a 2.2 percent maintenance cost to replacement asset value (RAV). Its overall equipment effectiveness (OEE), the metric for equipment availability, performance and quality, is approaching 90 percent.
This improvement is a long way from where the journey began in the 2004-2005 timeframe:
…maintenance expenditures were $480,000 to $500,000 per month, resulting in a maintenance cost to RAV or 6.5 percent… Higher maintenance costs were destroying profitability; moreover, the unreliable nature of the facility created undue pressure on the facility’s staff, to the point of demoralization.
Ultimate goals were established:
…of 1.6 percent OEEf. OEEf is OEE plus issues in operations’ control, such as non-quality losses, speed losses, operational failure, equipment failure and functional losses.
Run to failure was the common practice which created urgency to get equipment back online quickly. This did not provide many opportunities to perform root cause analysis on the failure mode, and in many cases:
…equipment ran to failure over and over on preventable uses, simply because the maintenance team was too busy for proper equipment failure analysis.
This run-to-failure culture created overtime pay opportunities for technicians which did not incentivize preventive and predictive reliability approaches.
…Corbion needed to the plant’s run to failure culture to a why did it fail culture.
The change began by:
…holding team meetings and increasing training to help employees on every level understand that instead of simply fixing problems, they need to prevent them. Operators and maintenance technicians were encouraged to find the root of the problem and think about solutions… Technicians are encouraged to follow the chain of consequence and, more importantly, thoroughly document their discoveries in the computerized maintenance management system (CMMS).
This data provided a historical record for analysis and prevention. A new compensation structure was also developed:
…that rewards reliability rather than failure by incentivizing the staff for doing the job correctly… Moreover, Corbion tied product performance and product quality to the bonus structure, giving operators and maintenance technicians extra incentive to ensure all processes are running at peak performance.
The results from these changes were impressive, even in the first 2 years:
…maintenance expenditures were down to $230,000 per month, a more than 50 percent reduction, resulting in an immediate savings of nearly $3 million…
These early results provided the lift to sustain and build the program. Reactive activities have shifted to planned activities, as the plant:
…now fully plans two weeks ahead with parts and three weeks ahead for work orders on equipment. As a result, the plan is operating at 99 percent planned work for its maintenance crew.
This planning not only reduced maintenance costs:
…2015 production is approximately 70 percent higher…
Read the article for more on Corbion’s path to reliable, more productive performance. You can also work with Emerson’s Reliability Consulting team to develop a comprehensive plan and measures of success for your organization to achieve top quartile reliable performance.