Artificial intelligence (AI) and machine learning (ML) are rapidly changing the way organizations leverage analytics. These systems enable complex analysis that human beings simply cannot perform manually, making it possible to solve difficult problems and identify actionable strategies to improve production, efficiency, sustainability, and safety.
Undergirding this analytics solution is a powerful technology stack. In a recent article in Control Global, Nicolas Lazare and Phil Nelson of XPS Expert Process Solutions (XPS) shared four key strategies they used when working with Emerson to implement an analytics solution.
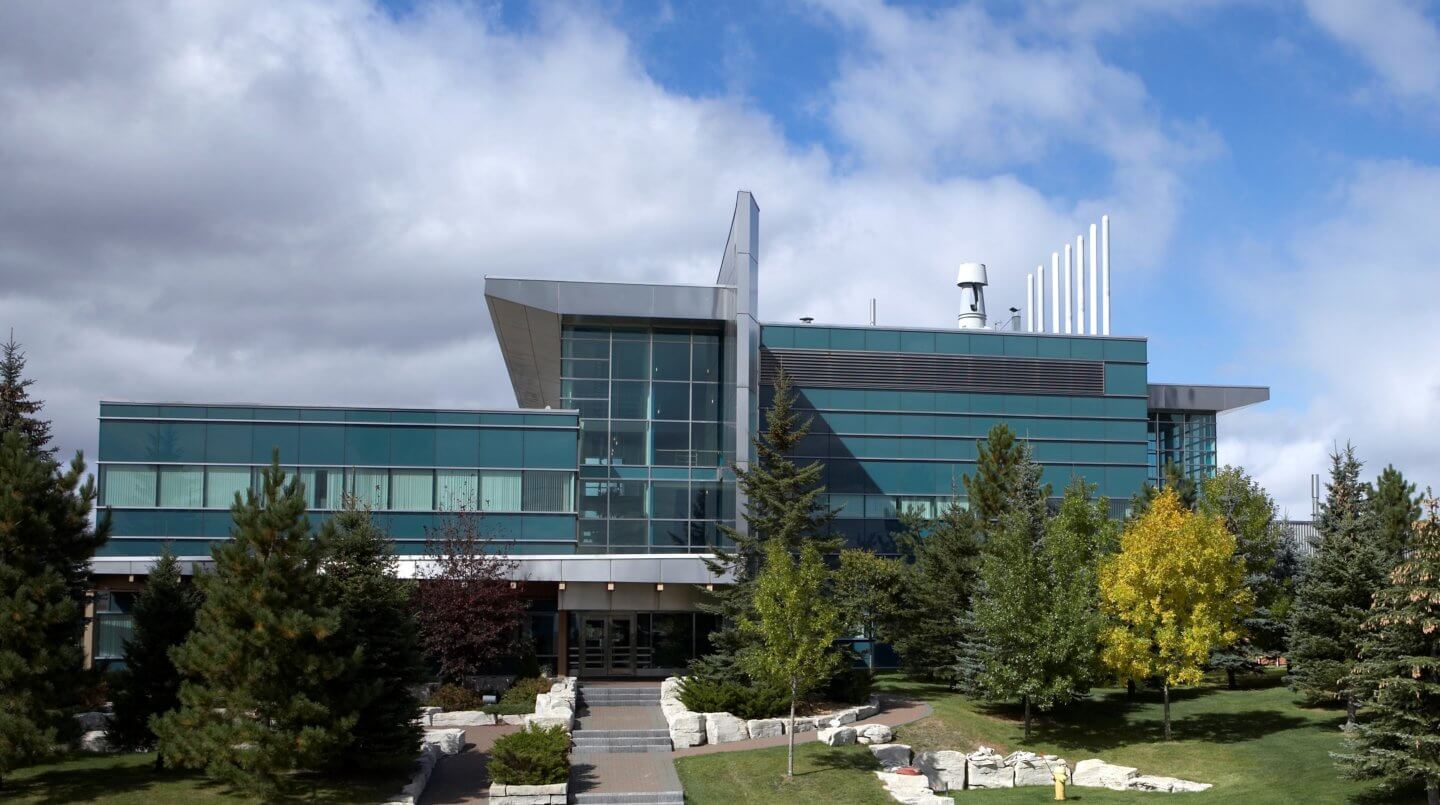
Expert Process Solutions building situated at 6 Edison Road, Falconbridge, Ontario inside Sudbury’s rich mining basin.
Selecting the right system
One of the earliest stages of the XPS analytics project—system selection—was also one of the most intense. The implementation team benchmarked ten different systems to ensure they found the right solution.
The process of benchmarking so many systems was time consuming, but it provided benefits that quickly offset the invested time and effort. Team members could see the advantages and limitations of each solution, not only as a list of software features, but as they actually applied to XPS clients’ production.
XPS selected Plantweb™ Optics Analytics for its ability to use AI and ML for multivariate analysis that detects abnormal behavior in real time to identify current issues and predict future performance. Strong out-of-the-box models coupled with powerful rules logic and robust FMEA enabled engineers to use the models they already knew were successful and easily create new models to add capability as necessary. This meant XPS could see results, and return on investment, right out of the gate.
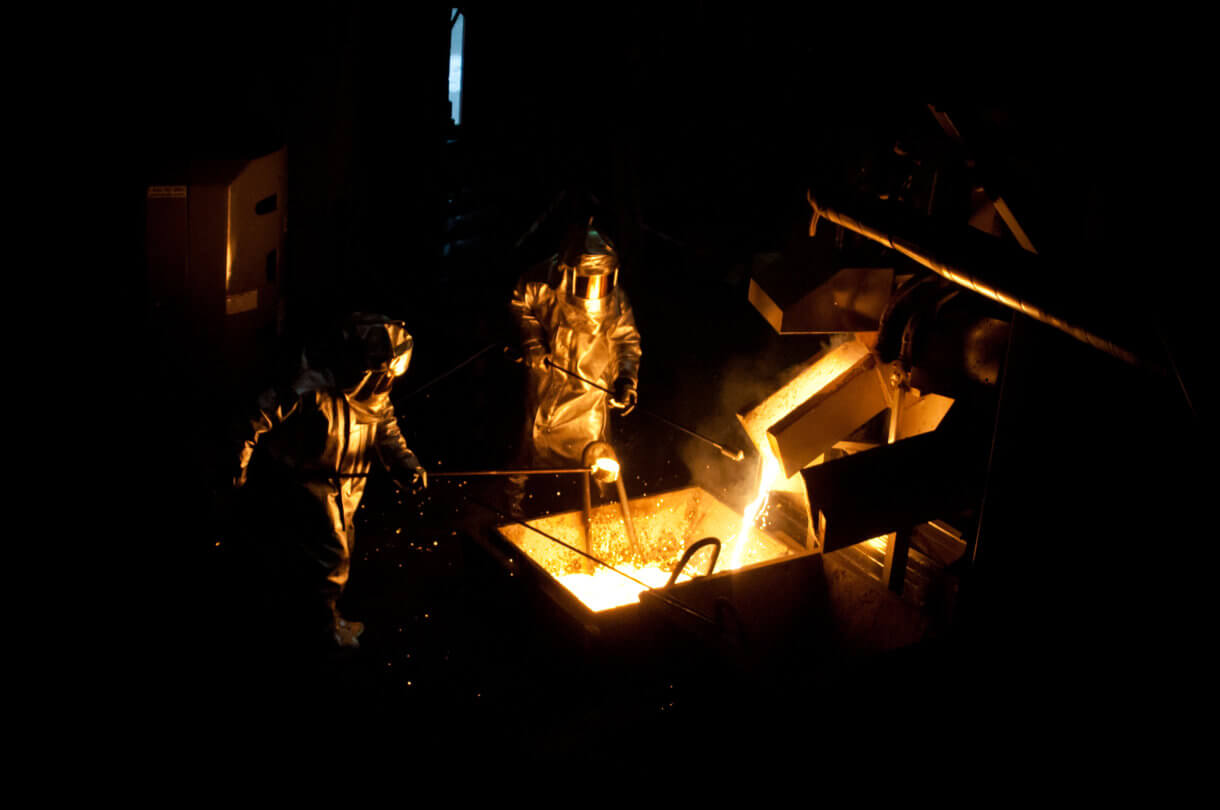
An extractive metallurgy test campaign showing tapping and sampling of the DC Furnace operated by XPS
Ensuring interoperability
XPS provides services for many organizations across the metals and mining industry. The company doesn’t get to choose the control systems it will need to work with on any given project.
To avoid adding complexity to the XPS architecture, one of the most critical benchmarks for the new analytics system was vendor neutrality. The team specifically searched for a platform able to integrate with a wide variety of control systems, historians, and other information sources out of the box without custom engineering.
Selecting Plantweb Optics Analytics, which can connect to a wide range of third-party systems out-of-the-box, will save XPS a great deal of time as it avoids the need to add complexity of engineering custom interfaces for every project.
Selecting the best analytics
As they evaluated analytics packages, the XPS implementation team was looking for something very important: any chosen package would need to support both XPS’s existing models and would need to make it easy to create new models on demand.
The best systems were the ones which enabled engineers to build or use existing algorithms or rules offline, test them, and then move them to an online system when the team confirmed success. Truly robust systems avoided the need for the team to start from scratch—combining unique XPS knowledge with key out-of-the-box solutions without sacrificing best practice engineering.
The team took the time to run old models side-by-side with new models. While this process was time consuming, it allowed the team to be certain the new models performed as well as expected.
Identify the wins, big and small
The XPS implementation team was not afraid to put its potential technologies to the test—and that forward-thinking policy paid off. In one instance, the team used its analytics package during a training session as a trial and ultimately managed to solve a problem that had been vexing the organization for some time.
During a software training session, the team decided to use the pumping issue as a trial. Once a dataset was collected and organized, the team was able to identify in less than an hour that slurry density was the other contributing factor to the observed behavior using Optics Analytics’ multivariate analysis capabilities.
In addition to fixing a critical pumping and thickener issue during their training session, the XPS team saw a wide range of benefits from implementing Plantweb Optics Analytics. The team also quickly developed newer, more robust asset control models and digital twins to control and optimize, in real time, metallurgy of assets such as furnaces, converters, and reactors. They improved operator reaction time and accuracy with a single-screen dashboard that more rapidly draws operator attention to production aberrations. The entire XPS team can now quickly get to the root of problems and solve them, rather than spending time addressing only the symptoms.
To learn more about how XPS developed a robust analytics program you can read the whole article. You can also learn and discuss more about how multivariate analysis through AI and ML helps plants shorten the decision-making process by visiting the Emerson Exchange 365 community pages.