Maximize product quality batch after batch
The food and beverage industry continually face market challenges due to increased demand for product differentiation, while trying to improve operational efficiency and reducing costs. Meeting these needs requires balancing profitability of core products without reducing productivity in others. Companies must seek new ways to achieve operational excellence to remain competitive in today’s rapidly changing environment.
Food and beverage manufacturers must keep up with consumer demand for core and new products to stay competitive
Manufacturers are faced with demands to increase capacity and reduce production costs while demonstrating environmental stewardship. This can be challenging due to an evolving market conditions that require high levels of quality and increased product variety.
Food and beverage Solutions to address The Market Challenges Using a Measurement Solutions Approach
Maximize production to meet market demands
With significant shifts in consumer preference toward more unique solutions, manufacturers must find ways to reduce changeover time while driving efficiency to maximize production. Technology plays a large role in increasing flexibility and providing critical insights for operations to increase throughput and meet market demands.
Improve quality while minimizing loss
Consumers expect the highest quality when it comes to food and beverage products they purchase. Automation has driven product variability down over time, but even with these improvements it can still take extensive time for producers to respond to quality issues. Measuring quality parameters on-line can help address issues before “out-of-spec” products are created. Minimizing out-of-spec product and preventing errors from leaving the plant are critical for improving quality and reducing regulatory compliance risks.
Increase reliability to achieve production targets
Manufacturers are driven by consumers not only to maintain high levels of consistency with existing products, but also to develop and deliver new, experimental products. Maintaining product consistency and running new production lines requires reliable operations to remain competitive and deliver returns to fund new developments. Increasing reliability means reducing the frequency, duration, and impact of planned and unplanned events. It is critical in achieving production targets and reducing costs.
Effectively clean process equipment with enhanced procedures
Clean-in-Place (CIP) procedures certify that process equipment and pipework are clean/sterile and ready for the next process to be run. CIP processes can present measurement challenges which induce energy loss and create waste that ultimately lead to higher operating costs. Emerson’s measurement instrumentation provides the most accurate, reliable, and long-lasting technology to ensure your process equipment is clean/sterile and ready for the next process to be run.
Emerson Introduces World’s First Non-Contacting Radar Level Transmitter Designed Specifically for Food and Beverage Applications
Besides leveraging existing measurement solutions portfolio to meet the toughest challenges, it is important to continue to innovate and build capability to meet future Food & Beverage challenges.
To meet the need for highly accurate and reliable level measurement in hygienic applications, Emerson has developed the Rosemount 1408H Level Transmitter, the world’s first non-contacting radar device designed specifically for the food and beverage industry. Dedicated features include a hygienic compact design, fast sweep technology, exceptional radar beam focusing and IO-Link communications, helping manufacturers to optimize the efficiency of their operations, reduce product losses and ensure food safety.
Non-contacting radar is an ideal level measurement technology for applications that require stringent hygienic facilities and equipment. It is virtually maintenance-free, which helps it to ensure long-term reliability, in sharp contrast to legacy technologies. It has a top-down installation that reduces the risk of product loss through leakage, and it is unaffected by process conditions such as density, viscosity, temperature, and pH. The compact and robust form of the Rosemount 1408H makes it a suitable solution for the small tanks and space-constrained skids commonly used in food and beverage production. The hygienic antenna is flush with the process connection that ensures the removal of process residue during clean-in-place and sterilize-in-place processes and is insensitive to condensation and build-up. The hygienically approved, IP69-rated device has a stainless-steel housing with minimal crevices to withstand external washdowns and ensure cleanability.
The Rosemount 1408H is the first non-contacting radar transmitter with connectivity to the IO-Link communication protocol, making it easy to integrate with any automation system. The transmitter provides both conventional 4-20 mA, switch outputs and digital high-speed communication. It features innovative technology and smart algorithms to ensure installation and commissioning are made easy, saving time, and helping ensure trouble-free operation. Together with the new Rosemount IO-link Assistant software, which sets the parameters via IO-link, the experience of using Rosemount IO-Link devices is enhanced even further.
How the Rosemount 1408H Level Transmitter Addresses Key Food & Beverage Challenges:
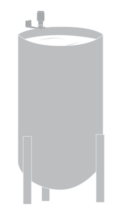
The 1408H Level Transmitter minimizes waste by giving you the most accurate level measurement no matter how low the product in the vessel
Reduce Product Losses
The Rosemount 1408H uses Frequency Modulated Continuous Wave (FMCW) technology and smart algorithms to maximize measurement accuracy and reliability, even in small tanks and challenging fast-filling vessels. Non-contacting radar technology is ideal for applications in the hygienic industry as it is maintenance-free, has a top-down installation that reduces the risk of leakages, and is unaffected by process conditions such as density, viscosity, temperature, pressure, and pH.
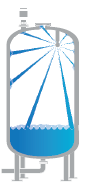
The 1408H Level Transmitter Reliable level measurement during and after cleaning (CIP – Clean in Place), plus optimization of cleaning agent storage.
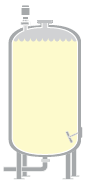
The 1408H Level Transmitter ensures correct filling and storage levels in tanks with agitators in Dairy & Food Beverage Operations
Maximize Production Capability
Foaming liquids or turbulence may cause weak and varying surface echo amplitudes. Surface turbulence is not normally a problem unless it is excessive. Measurement in foamy applications depends largely on the foam properties. When the foam is light and airy, the actual product level is measured. For heavy and dense foam, the transmitter may measure the level of the foam’s upper surface.
Ensure Product Safety
The Rosemount 1408H is a transmitter for continuous level measurements in the hygienic industry. The measurement principle is fast-sweep Frequency Modulated Continuous Wave (FMCW). The transmitter continuously emits signal sweeps with a constantly varying frequency towards the product surface. Since the transmitter continuously changes the frequency of the transmitted signal, there will be a difference in frequency between the transmitted and the reflected signals.
Emerson’s measurement instrumentation portfolio applies industry expertise and innovative solutions to your business challenges. Our global network of resources and service capabilities is the partner of choice for companies like yours. We have the expertise to help you dependably define, execute, and support your service strategy throughout the lifecycle of your operation while ensuring your workforce is up to the task.