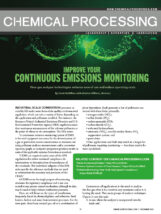
This Chemical Processing article looks at how new gas analyzer technologies optimize emissions monitoring in chemical plants and refineries.
It is difficult to find a process industry application that doesn’t burn some kind of fuel to generate heat. And where there’s combustion, environmental regulators won’t be far behind because industrial-scale fired heaters, boilers, and other processes invariably require monitoring and reporting. Determining what is going out of the stack usually calls for a continuous emission monitoring system (CEMS), with one or more gas analyzers to quantify the pollutants of interest.
CEMS Types
Since there are so many possible applications, there are many ways to perform the necessary measurements. The requirements for a coal-fired rotary kiln are much different from a fired heater burning natural gas in support of a distillation column, hence there are five main categories of measurement techniques. Installations burning natural gas or fuel oil are the most common, and those are the ones highlighted in this Chemical Processing magazine’s article by Emerson’s Katherine Williams and David McMillen. The article looks at the CEMS options for refineries and chemical plants and compares cold/dry CEMS to hot/wet CEMS. Special focus is given to how hot/wet extractive CEMS addresses problems that emerge due to the composition of flue gas, especially from one primary component: water.
As it leaves the stack, flue gas primarily comprises nitrogen, residual oxygen, various pollutants, and a lot of water vapor (8 – 20%). Because the gas is hot, typically >95°C (>200°F), its ability to carry water vapor is greater than air at the ambient temperature. Therefore, the dew point of the flue gas generally is below its exit temperature but higher than the ambient temperature, so water condenses as it reaches the atmosphere.
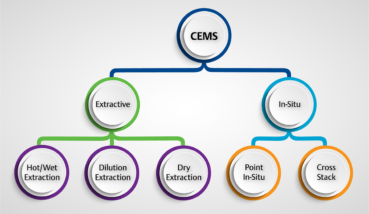
Extractive and in-situ methods can provide continuous emissions monitoring but in-situ approaches suit only a small segment of applications.
CEMS Challenges
Some gas analyzers don’t handle liquid water well, so sample conditioning methods chill the sample gas until the moisture condenses and can be removed before reaching the analyzer. This cold/dry method is very common, but it is complex and maintenance-intensive because handling the water is a challenge, and the condensation process affects some pollutants. The alternative is to keep the gas sample hot so water remains as vapor, provided the analyzer can handle high-temperature gas.
As analyzer technologies have evolved, some have become more tolerant of higher operating temperatures, making the need for chilled gas samples less important. This has helped launch a simple and effective sampling technique that is becoming more widely used: a hot/wet system. A single sample stream flowing directly from the tap point to the analyzer without passing through a chiller. The sample stream is maintained as hot as necessary to keep all components above their dew point, so no condensation occurs.
Avoiding Complexity
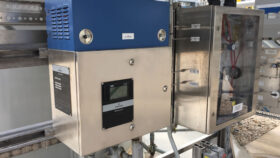
Laser-based gas analyzers such as the Rosemount CT500 Continuous Gas Analyzer can handle sample gas temperatures up to 190°C (375°F), making them well suited for hot/wet CEMS systems.
Keeping the sample hot delivers it in its most unadulterated form to yield the most accurate readings because there is no need to compensate for changes caused by cooling and moisture removal. Emerson’s Rosemount CT5100 Continuous Gas Analyzer is the first Quantum Cascade Laser (QCL) system developed for process gas analysis and emissions monitoring. The CT5100 is available in two variants: a certified system, housed in a purged and pressurized enclosure for hazardous area installations, and a non-certified system for use in non-hazardous areas. Both can house up to six lasers to measure multiple components in the gas stream simultaneously. It can handle gas samples up to 190° C (375° F), higher than the dew point of water and most acid gases. This eliminates the need for gas chillers, permitting a much simpler sample handling system.
Check out the article for a case study on how a U.S. refinery used the Rosemount CT5100 to optimize emissions monitoring and fulfill one key company objective—reducing the amount of maintenance attention required with previous CEMS approaches.
Visit the Gas Analysis pages at Emerson.com for more on technologies and solutions for quality and content evaluation. You can also connect and interact with other engineers in the Chemical and Oil & Gas Groups at the Emerson Exchange 365 community.