Chemical plants are hazardous environments that rely on safety instrumented systems (SIS) to protect personnel, assets and the surrounding area. Perhaps surprisingly, decades-old SIS are still in use at many plants, with organizations adopting an attitude of ‘if it isn’t broken, don’t fix it’. However, in a Chemical Processing article, ‘Upgrade Your Safety Instrumented Systems’, Emerson’s global functional safety manager AnnCharlott Enberg explains that upgrading to modern SIS instrumentation would enable companies to enhance safety and lower lifecycle operating costs.
The article reveals that organizations are reluctant to upgrade their measurement devices because they believe it would be costly and complex to do so. However, as AnnCharlott explains:
…to reduce complexity, the latest flow, level, pressure and temperature measurement devices suitable for integration into a SIS have been designed to ease their installation and use. Crucially, they feature enhanced functionality that provides a range of significant benefits, such as smart diagnostics suites and remote proof-testing capabilities. This functionality helps increase plant and personnel safety, and decrease maintenance costs and downtime, which typically leads to a quick return on investment.
The article lists some specific aspects of enhanced functionality in modern SIS instrumentation and the significant benefits it can achieve. It begins with proof testing of level measurement devices, which is necessary to verify that equipment will work correctly when a safety demand arises. Two types of proof test – comprehensive and partial – can be performed in compliance with the IEC 61511 and API 2350 standards relating to functional safety. Comprehensive proof tests involve testing an entire safety loop in a single procedure, to return its probability of failure on demand (PFD) back to, or very close to, its original level. Partial proof tests can include one or several parts of a safety loop and will bring the PFD of a device back to a percentage of the original level. As AnnCharlott explains:
…Performing a partial proof test can provide significant benefits. Such a test is quicker to complete, interferes less with operations and, crucially, justifies an extension of the time interval required between comprehensive tests while remaining within regulatory requirements. This extension may allow scheduling the comprehensive test during a planned shutdown, thus increasing plant availability and efficiency.
Proof testing has traditionally occurred on location but the digital technology available in modern level measurement devices enables partial proof testing to be performed remotely. The article states:
…the devices remain installed while simulated overfill conditions activate the detector and generate an alarm signal. Use of simulation makes moving fluid into and out of the tank to conduct the test unnecessary and avoids the risk of spills. It also eliminates the need for workers to climb tanks or be exposed to tank contents, thereby increasing their safety and freeing them up to concentrate on other value-added tasks.
The article then describes how advanced diagnostics in modern pressure transmitters can detect many abnormal conditions in processes, including plugged impulse lines. Impulse lines are the small-diameter tubes or pipes that transmit the pressure signal from the process to the transmitter. When they become plugged with solids or frozen fluid in cold environments, this blocks the signal and results in the transmitter continuing to provide the same pressure reading as before the blockage. This will then be a misleading measurement that can compromise safety. To meet this challenge, a statistical processing technology has been developed that enables early detection of abnormal situations, including plugged impulse lines, in a process environment. AnnCharlott explains:
…The technology is based on the premise that virtually all dynamic processes have a unique noise or variation signature when operating normally and that deviations in these signatures may indicate a significant change in the process, process equipment or transmitter installation will occur or already has.
AnnCharlott continues:
…The sensing of the unique signature begins by using a high-speed sensing device combined with software to compute statistical parameters that characterize and quantify the process noise or variation. This enables the device to detect significant changes in process noise or variation and then communicate an alarm notifying operators of an abnormal situation. Such early warning allows maintenance technicians to resolve the issue before it affects safety.
The article continues by stating that in some applications, monitoring for changing liquid surface conditions is critical in preventing overfills. To help monitor changing surface conditions, the latest radar level transmitters include diagnostics based on signal quality metrics.
AnnCharlott explains that:
…signal quality values range from 0 to 10, with 10 representing a strong signal and no process noise. A significant change in the signal quality value might indicate changing surface conditions. For instance, if foam is present, the signal quality would drop in value. By sending level and signal quality to the control room as process variables, operators there can monitor these parameters over time. Crucially, this can enable the operators to quickly recognize an unwanted surface change, thus increasing safety by reducing the risk of tank overfills caused by these conditions.
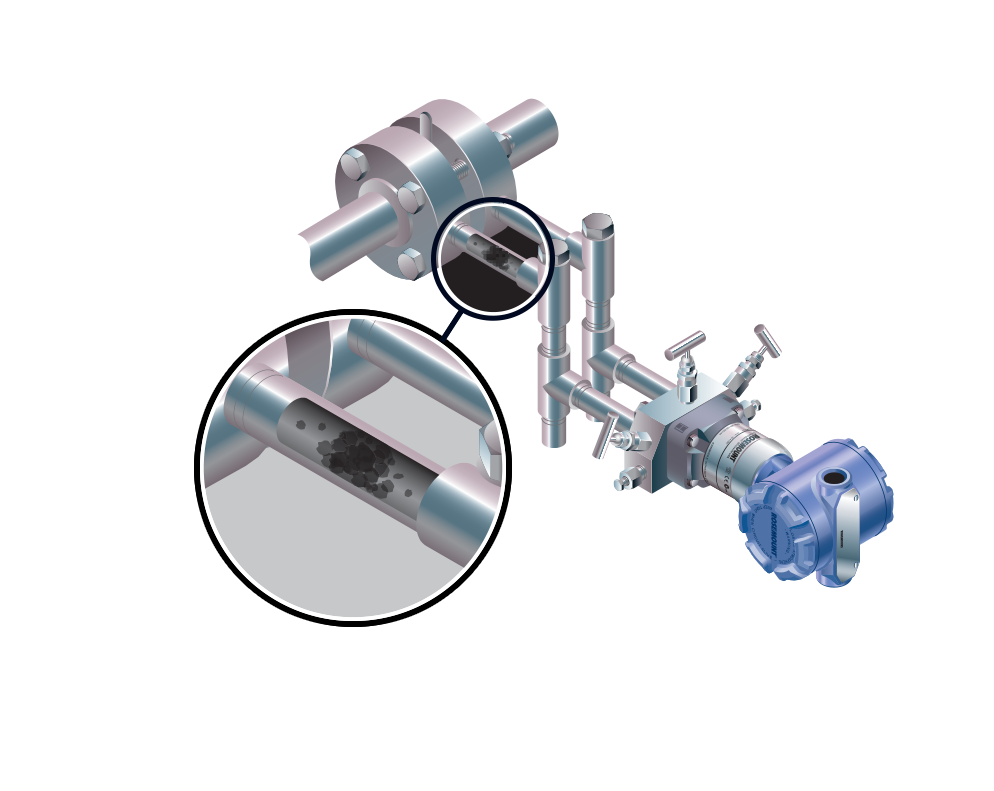
Small-diameter tubes or pipes used with pressure sensors can fill with solid material or freeze in cold environments.
It is important that the magnetic flowmeters used in a SIS operate accurately, as failure can lead to a process shutdown, reducing throughput and profitability. However, issues can sometimes arise, with the leading cause being improper grounding and wiring. This allows the electrodes to pick up electrical noise and, consequently, affects the signal-to-noise ratio and the stability of the transmitter output. AnnCharlott explains that:
…Modern devices feature a ground- and wiring-fault detection diagnostic. If the installation is not grounded or wired properly, the diagnostic will activate, delivering an alert to carefully review the grounding and wiring of the installation. It also can detect if the grounding is lost over time due to corrosion or another root cause.
The article then describes how the latest temperature measurement devices feature advanced diagnostics that alert users to a degraded sensor or installation condition before measurement failure occurs. It adds:
…Some transmitters feature the capability to provide temperature measurement redundancy, thereby increasing safety; the transmitter automatically sends a maintenance alert during primary sensor failure and switches the output to a secondary sensor without impacting the measurement signal.
Visit here to learn more about Emerson’s range of measurement instrumentation certified for use in SIS. You can also connect and interact with safety experts in the Measurement Instrumentation group in the Emerson Exchange 365 community.