Duke Energy’s Heat Recovery Steam Generator Engineer Eugene Eagle and Emerson’s Director of Steam Conditioning Group Justin Goodwin recently published an article in the February 2022 edition of Power Engineering. The article is titled How Duke Energy Addresses Attemperator Issues, and it describes the deployment of a new steam atomization attemperator design that allowed Duke to reliably and safely run their combined cycle units at very low load conditions. A summary of the article follows.

Figure 1: An attemperator is usually installed between the primary and secondary superheaters and/or reheaters in a combined cycle plant. It injects water to control the HP superheater or hot RH steam outlet temperatures.
Controlling steam temperature in the various stages of a combined cycle plant is a challenging task, particularly during startup, shutdown, and major load changes. Under these conditions, the exhaust steam temperatures can rise precipitously, so attemperators are often installed between the primary and secondary superheaters and reheaters to address this potential issue. These devices inject water into the steam, and they control the high-pressure (HP) superheat and hot reheat (RH) outlet temperatures (Figure 1).
While this arrangement has worked well for plants in the past, new process demands are causing problems in some applications. The authors explain:
Many combined cycle power plants were originally designed for base load power generation. However, due to intermittent power generation from solar and wind sources, combined cycle plants are increasingly used to level the power generation profile. This forces some combined cycle units to operate across a wide band of varying load conditions, known as load following.
As the generating load adjusts to meet demand, the gas turbine (GT) exhaust temperatures and heat transfer rates in the heat recovery steam generator (HRSG) also change. This can create rapidly rising steam temperatures that will exceed equipment ratings if not properly controlled.
Attemperators are carefully selected for the expected range of process conditions, but as the power generating landscape changes, many combined cycle plants are asked to operate at very low power generation rates. GT manufacturers have evolved their technology to match these low load ranges, but the resulting range of dynamic process conditions is stretching many attemperators beyond their capabilities.
Attemperator challenges
Attemperators have the seemingly simple task of spraying enough water into the steam flow to control the temperature. Unfortunately, this is much more difficult than it might appear, and when done incorrectly, significant damage can result (Figure 2).
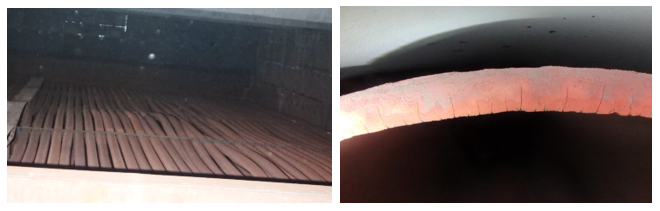
Figure 2: Damage caused by poor performing attemperators can include warped tubes (left), along with cracked attemperator liners (right) due to quenching.
The authors describe the attemperator process:
An attemperator controls steam temperature by injecting a spray of very fine water droplets into the steam flow, and these droplets should ideally evaporate immediately. The evaporating liquid reduces the steam temperature, and if the water droplets do not hit the extremely hot pipe walls, the process works well. Unfortunately, attemperators often do not function as designed, and significant problems often result.
Some of the typical problems include:
- Large droplets from malfunctioning spray nozzles fail to evaporate and impinge on the walls of the pipe. This creates thermal shock, causing stress cracking. Liquid water can also enter secondary superheater or reheater tubes and warp them (Figure 2, left).
- When attemperators cycle off and on, they can encounter thermal fatigue and mechanical failure. Probes can also fail when high steam velocities set up vortex shedding around the probe and vibrate it to failure.
- Leaking attemperator spray block valves will drip water into the pipe, leading to cracking of the internal liner (Figure 2, right)
- Spray nozzles stick open or shut, affecting spray patterns or flow characteristics.
Different designs have been applied to address these issues, with varying degrees of success. It is easy enough to design an attemperator that operates well in a narrow range of steam flows and water flows. Unfortunately, changing process unit generating loads require an attemperator to operate across a much broader set of steam flow, water flow, and pressure drop conditions—posing significant engineering challenge.
Spring-loaded spray nozzle designs (Figure 3) handle a wider range of nozzle pressure drops, while still atomizing the water as required.
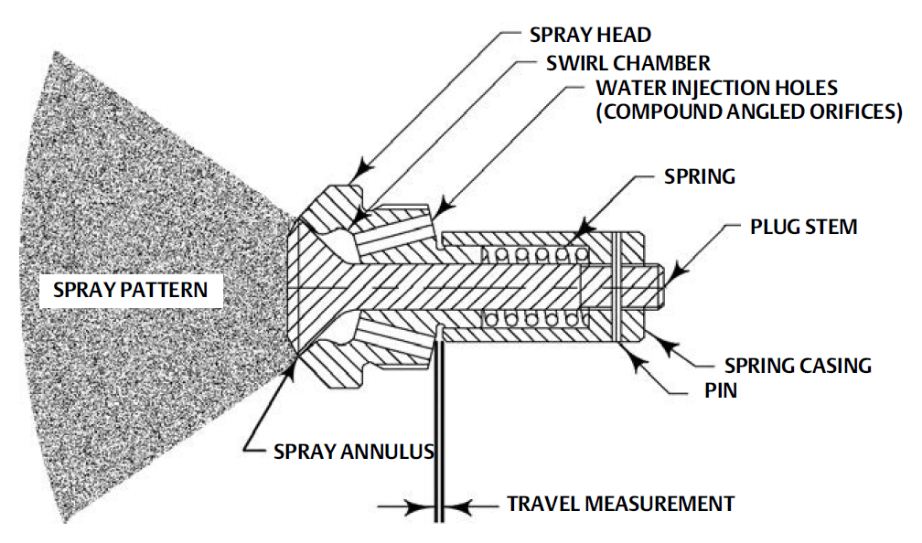
Figure 3: A spring-loaded attemperator nozzle can handle a wider range of flow and pressure drop conditions, while still effectively atomizing the water passing through it.
While these designs certainly provide improved performance with varying load conditions, the rangeability requirements of some combined cycle plants are stretching even these nozzles past their operating limits. Multiple thermocouples are often installed in the steam piping downstream of the attemperator to detect developing problems. If these measurements approach the saturation temperature of the steam, or if there is a wide variation of temperature readings, this indicates a probable attemperator issue.
A problem at Duke Energy
One of Duke Energy’s combined cycle power plants in North Carolina was having issues with their ring-style, spring-loaded nozzle attemperators. The plant’s generating load was varying dramatically, and the plant often operated under low load conditions when the GT exhaust gas temperatures were highest.
The existing attemperators were unable to control temperature because they faced a perfect storm of process conditions. The low GT load and higher resulting exhaust temperatures produced lower reheat steam flows and steam pressures, yet these conditions required very high attemperator spray flow rates.
Normally the turbulence of high velocity steam flows helps dissipate and evaporate water droplets from an attemperator. But at low load, the reduced steam density and flow cannot easily evaporate the water. The situation is made worse by the increased water flow required to quench the rising temperatures.
Downstream thermocouples indicated significant overspray and thermal shock. Analysis predicted crack initiation in another 4.7 years of operation. The problem was expected to worsen as Duke Energy brought more solar capacity into their grid.
Plant personnel began searching for alternative attemperators. Eugene and Justin described the ultimate solution:
Emerson engineers worked with Duke Energy plant and regional engineering personnel to develop a hot reheat steam atomizing attemperator. Steam was sourced from the high-pressure steam system (Figure 4) with no fabrication joints, shrink-fits, threads, or other joints within the nozzle. Emerson also found a way to fit the solution into the existing attemperator body, avoiding significant field piping rework.
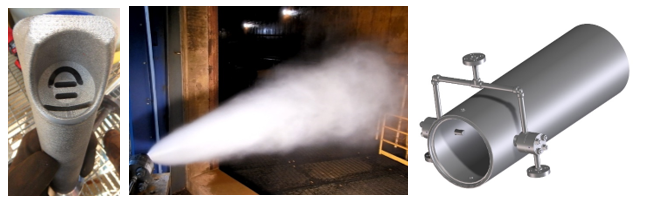
Figure 4: High pressure steam is injected at the flow nozzle (left) to completely atomize the water under a wide variety of water flows and process pressures (middle). The steam-atomized attemperator (right) was designed as a retrofit to the existing spring-loaded nozzle attemperator to minimize piping changes.
A small amount of steam from the high-pressure steam drum outlet was piped to the new attemperator and injected at the nozzle to atomize the water into a fine mist, which readily evaporated in the steam line regardless of flow. This allowed the new design to maintain very high performance across a wide range of process steam and water flow conditions.
Dramatic Results
The new steam atomizing attemperator was installed at one of Duke Energy’s combined cycle power plants as a trial. The authors described the result:
The process improvement was immediate and significant. Figure 5 shows a side-by-side comparison of the thermocouples downstream of the attemperator as the gas or combustion turbine (CT) load (indicated by the light blue line at the bottom of the graph) increases from a low to normal load condition.
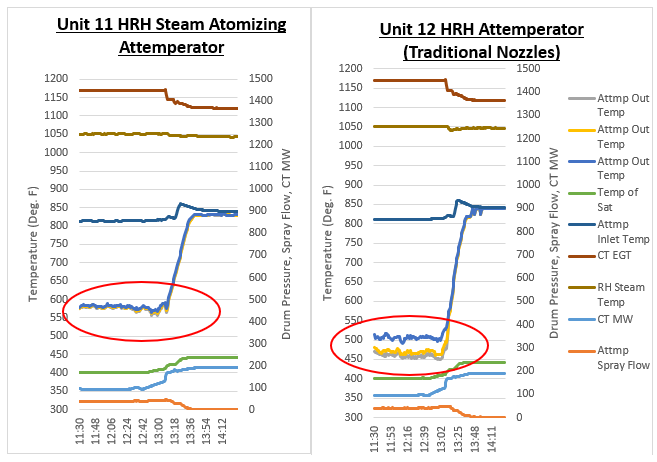
Figure 5: The results of the field trial are indicated here. The graphs on the left show the new steam atomizing attemperator operating under a low- to high-load transition versus the traditional nozzles on the right. The circles highlight the absence of variable temperature readings downstream of the new attemperator and show how the new design maintains the outlet temperature much further from the green saturated steam temperature line.
After evaluating the field trial results, Duke Energy chose to upgrade the hot reheat attemperator in the second unit of this 2×1 CC power block to the new steam atomized design. Duke Energy has also completed the same upgrade at a 2×1 CC sister site, as well as executed a replacement project to remove and replace two HRH attemperators at a third power station.
Visit the Steam Conditioning and Desuperheating section on Emerson.com for more on the technologies and solutions to improve steam system performance.