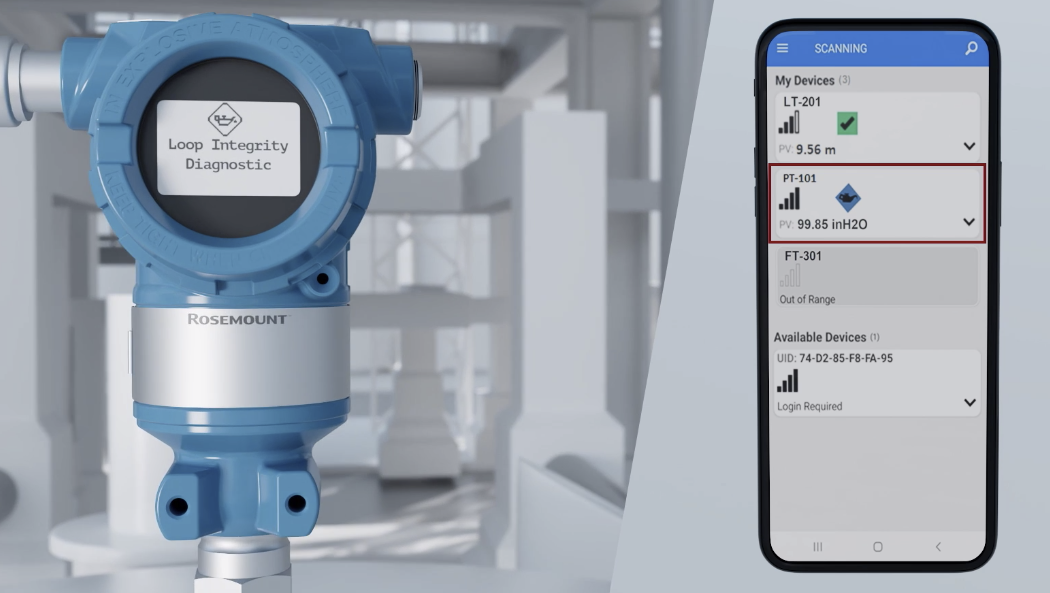
In a Hydrocarbon Processing magazine article, Emerson’s Megan Wiens explains how adding Bluetooth technology to individual instrument transmitters improves communication and safety.
One of the first industrial uses of Bluetooth technology was from PLC vendors. The key selling point was that once the PLC was installed in its cabinet and everything was connected and working in the plant, there were understandable safety concerns about opening the cabinet. With this new communication option, a troubleshooter wanting to tweak the program could do it by connecting wirelessly from a laptop without a cable, avoiding shutdown and safety problems.
Bluetooth technology has evolved and improved, and it is now practical to utilize it in individual process instrument transmitters. How this is being applied is the topic of my article in the April issue of Hydrocarbon Processing, How Bluetooth Technology Extends the Capabilities and Connectivity of Wired Instrumentation.
Options have been selected within the Bluetooth technology offering to make it suitable for industrial environments so it can be applied to field devices mounted in process manufacturing facilities. Using this approach, Bluetooth wireless communication is being added to a growing variety of field devices as a method for easy configuration and viewing of information via proprietary plant asset management software. This type of bidirectional communication empowers technicians to access data and change configurations as needed without a wired connection.
One of the first instruments where Emerson is adding Bluetooth technology are the Rosemount 3051 Pressure Transmitter family. This makes sense since this product, across all its forms, is Emerson’s largest selling instrument, and it’s where we have recently introduced some of our latest improvements, such as advanced diagnostics and our new enhanced local display.
So how does adding Bluetooth technology help on a day-to-day basis?
When an operator carries a laptop, smartphone or tablet equipped with the appropriate app, it will discover all Bluetooth enabled instruments within a radius of approximately 15 m (50 ft). These instruments “broadcast” their presence continuously, waiting for a technician to request a connection through the app. Since the instrument’s radio power consumption is very low, it operates using normal loop power.
Using an appropriate password, the technician can connect with the transmitter and access all the information wirelessly that would be available using a conventional HART communicator the old-fashioned way. Because a tech no longer needs to be next to the instrument, access is greatly eased, especially for instruments installed in hazardous or hard-to-reach areas. But there’s more:
If the technician needs additional documentation to carry out a specific task, it may be possible to access it for that specific transmitter directly from the Bluetooth app with an internet connection via the plant’s WiFi network, avoiding the need to go back to the control room or maintenance shop. These timesavers can expedite any required actions, allowing technicians to spend far less time in the plant environment.
For now, we’re using the HART communication methodology, the same as via an Emerson AMS Trex Device Communicator with leads. This shortens the learning curve for Bluetooth drastically as the techniques and menus are those technicians already know. But Bluetooth is about 10-times faster, plus, it does not have the same limitations as HART, so new and more intuitive techniques are also in the works.
For more information, please visit the Emerson Bluetooth® Connectivity for Field Instrumentation webpage. You can also connect and interact with other engineers in the Chemical Processing and Refining Groups at the Emerson Exchange 365 community.