The next P in our 5P’s series is Parts & Extended Warranty. This topic is often underestimated or even ignored, but effective Spare Parts management involves various factors that must inform your parts inventory decisions, as they can significantly affect your operating costs and uptime. We will examine these drivers and explore an integrated approach to optimize your spares.
FACTORS TO CONSIDER
Cost of Downtime
A direct and perhaps most significant cost of downtime in a manufacturing or process plant is decreased or lost production, resulting in lost revenue. But that is not all. Even when a plant is down, labor expenses are incurred as plant personnel remain onsite or on call. Having insufficient onsite spares prolongs this downtime and requires personnel overtime and expedited shipping. Moreover, prolonged or recurrent downtime can damage a plant’s reputation and lead to delivery/customer satisfaction issues.
Maintaining an inventory of onsite DCS spares is a proactive strategy to mitigate the effects of downtime. Having readily available controllers, I/O cards, workstations, and spare networking devices can help minimize these downtime costs by:
- Reducing time to repair
- Minimizing rush orders
- Improving maintenance flexibility (component swap-out as part of routine maintenance and troubleshooting)
- Lowering the risk of extended downtime (and reputational risks)
Time to Repair
Mean Time to Repair (MTTR) is a key performance indicator in manufacturing and process plants that reflects the time it takes to restore a system or equipment to operational capacity after a malfunction.
A primary strategy to improve MTTR figures is maintaining an onsite inventory of spare parts. As mentioned above, readily available replacement components lead to reduced downtime as maintenance teams can replace faulty components promptly. The team’s troubleshooting and diagnostic capability is also enhanced since having spares allows faster pinpointing of problematic components even before full-blown/catastrophic downtime occurs.
Reliability Intelligence
The importance of having onsite spares should be self-evident by now, but managing actual parts inventories and finding the right balance between operational continuity and inventory carrying costs is more complex.
This is where parts reliability information such as Mean Time Between Failures (MTBF) plays an important role.
While electronic component manufacturing variations, environmental and operating conditions, and system applications are what ultimately determine a particular equipment’s lifespan, MTBF data from equipment vendors and field reports can and should help you plan and calculate optimal onsite spare parts inventory. For instance, components with lower MTBF require higher stocking levels, while those with longer times between failures may not need as many spares.
Cost of Inventory
A spare parts strategy based on downtime tolerance, MTTR objectives, and component MTBF will help keep your inventory costs at bay. DCS spare parts can vary significantly, with some components requiring specialized storage conditions. Add this to warehousing, security, climate control, and personnel needed to manage said inventory, and you are looking at amounts that could eat into your annual Opex budget.
Obsolescence is another factor to consider. As you update the running system to keep up with the state of the technology, it becomes necessary to monitor the lifecycle status of your spares as well. You certainly wouldn’t want to be in a situation where that spare controller you believe you had no longer works with the version of software running on your control system.
AN INTEGRATED APPROACH
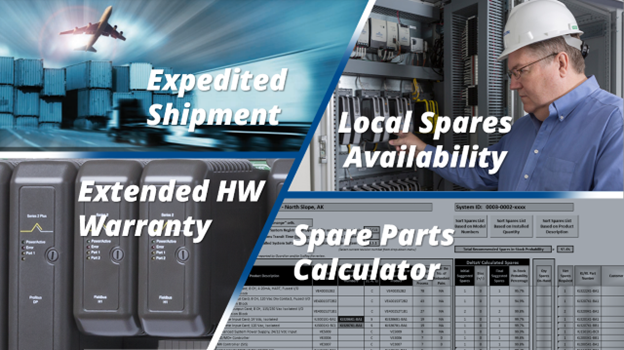
An Integrated Approach to Spare Parts Management
Emerson’s approach to enabling a responsive spare parts program for our customers is a combination of the following:
- Scientifically calculated onsite spares recommendation
- Local spares availability
- Expedited shipment capabilities
- Extended Hardware Warranty
Scientifically Calculated Onsite Spares Recommendation
Emerson service teams are equipped with a Spare Parts Calculator App. This is a game-changer for our customers as it combines intelligence, technology, and data analysis to provide guidance on the required number of spare parts for their distributed control systems.
The app integrates reliability intelligence, field failure rates, and product lifecycle information to come up with onsite spare recommendations. It also factors in the often overlooked elements like estimated import and customs transit times specific to each country, providing a holistic picture of spare parts procurement.
The app’s recommendations also consider the quantity of on-hand spares, allowing for continuous adjustments and optimizations. The output is an “In-stock probability percentage,”—which gives customers confidence that a part will be available should a failure occur.
Local Spare Parts Programs
Emerson’s local offices are our customers’ first point of contact should they need spare parts that are not readily available onsite.
These offices are directly linked to Emerson’s extensive inventory and resources, ensuring customers can quickly access the required parts. They also offer invaluable guidance to facilitate the purchasing process and cater to each customer’s specific needs.
Many offices are also equipped to provide tailored spare parts management programs. They collaborate with customers to understand their requirements, usage patterns, and maintenance schedules. This enables them to offer customized inventory management and delivery programs, ensuring customers have the right parts at the right time.
Expedited Shipment Capabilities
QuickShip by Emerson is a special delivery program designed to get parts and products to customers quickly. It uses our global network and local teams to keep systems up and running, even in unexpected situations, while managing costs.
In urgent situations, QuickShip Emergency puts a customer in touch with our dedicated reps 24/7. They’ll help pinpoint the right part, explore options, and swiftly process the order. Using our vast network and local support, they ensure the item arrives promptly.
For times when DeltaV Distributed Control System (DCS) or a DeltaV Safety Instrumented System (SIS) parts are needed faster than usual, QuickShip Expedite steps in. We’ll locate the nearest distribution center with the needed part and deliver it within a few business days.
Extended Hardware Warranty
The DeltaV Extended Hardware Warranty Service is designed to support the critical spare parts needed for the DeltaV Distributed Control System (DCS), Safety Instrumented System (SIS), or Standalone DeltaV PK controller system. By granting direct access to replacement components from Emerson, this service ensures that failed assemblies within an enrolled system can be replaced with either new or factory-repaired Emerson assemblies at no extra cost. These replacement assemblies come with a one-year warranty.
This service significantly reduces the need for onsite spare parts, allowing customers to allocate capital to other areas. It guarantees the availability of replacement parts from Emerson’s central parts depots, ensuring that shipments will be dispatched within one business day upon completion of the material-return process.
Taking a holistic and data-driven approach to spare parts management can minimize downtime, optimize costs, and ensure operational continuity. Emerson’s integrated programs offer a comprehensive toolkit for achieving control system resilience and peace of mind, empowering you to focus on what matters most – driving your business forward. ◼
◀ Part 3: Predictive Maintenance
Author’s Note
While the solutions linked above are mainly for Emerson DeltaV control system users, the concepts and principles should generally apply to any other Industrial Control System. If you want to learn more: