Sustainable aviation fuel (SAF) is a renewable alternative to the fossil fuels that have historically powered most aircraft. Compared to conventional fuel production, SAF production poses particular challenges for control valves. Below is a summary of our article in the August 2023 issue of Hydrocarbon Engineering, titled “Control Valve Selection for SAF Production,” which discusses these challenges and offers suggestions for selecting appropriate valves.
Overview of SAF
ASTM International first authorized commercial airlines to use certain biofuel blends in 2011. Demand for SAF is currently growing, especially as the government is now offering credits for both producers and consumers. Currently, most SAF is produced from lipids such as used cooking oil, plant oils, and tallow, because lipid conversion is similar to conventional refinery processes.
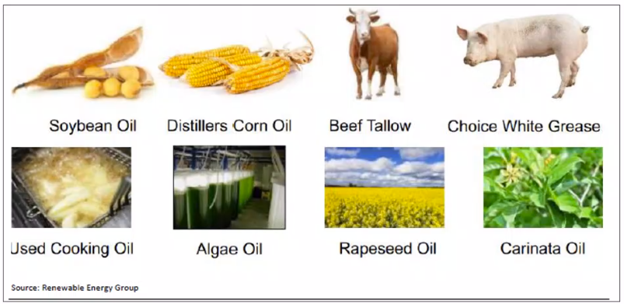
Nearly all SAF feedstocks must be pretreated, which involves contaminant removal and chemical conversion into intermediates suitable for hydroprocessing.
Challenging conditions
Following pretreatment, SAF intermediates are fed into hydrotreating and hydrocracking processes that are very similar to those used in conventional refineries. In these processes, some valves endure particularly grueling service conditions due to the unique qualities of SAF intermediates.
The intermediates tend to be more corrosive and stickier than with conventional feedstocks, and they are prone to paraffin and/or waxy build-up. The process also requires significantly more hydrogen, elevating process pressures and temperatures. Finally, the intermediate feed quality tends to be variable, so reaction chemistry is impacted and less consistent.
Proper valve selection is critical in these challenging conditions.
Pretreatment valves
Pretreatment control valves require corrosion-resistant alloy internals with unrestrictive flow paths, along with special coatings to prevent buildup and clogging. Rotary valves tend to shear away buildup during operation, extending service time between cleanouts.
Pretreatment valves
Like pretreatment valves, reactor feed valves must resist corrosion and buildup. They provide consistent flow to the reactor to maintain stable operation and extend catalyst life.
Pretreatment valves
Quench valves supply cooling hydrogen to control temperature in catalyst beds, extending catalyst life.
A post-guided unbalanced trim design will be less prone to sticking and can handle the temperatures and pressures of this service.
Once again, material selection is critical, as these valves are exposed to pressurized hydrogen and, potentially, to corrosive reactor materials.
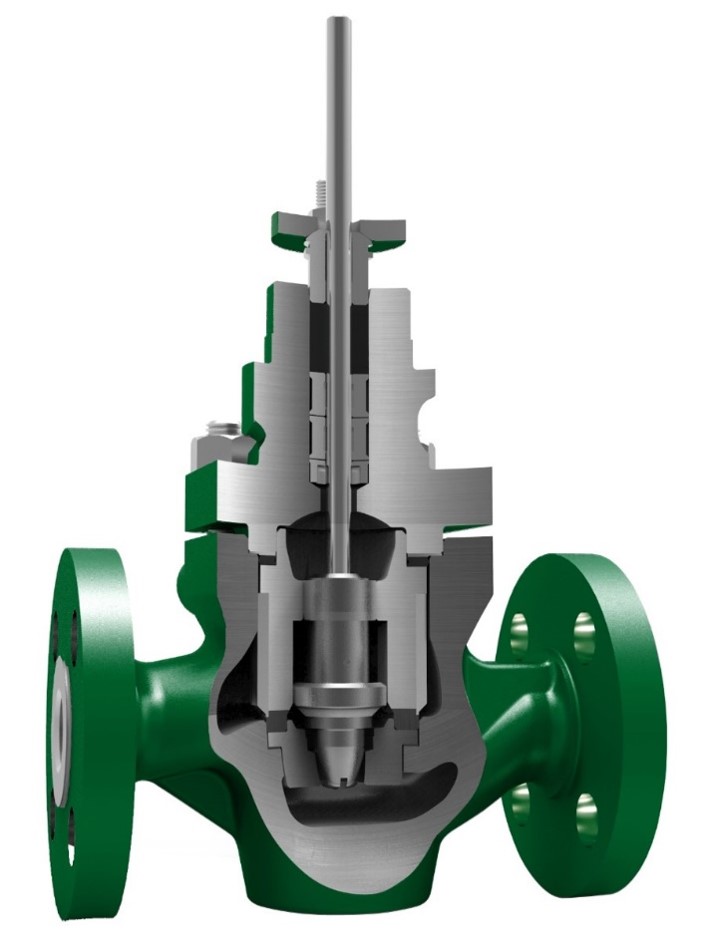
An unbalanced plug with tight shutoff is often employed in hydrogen quench valve service where product sticking/build up might occur. Material selection should account for the hydrogen service and possible corrosive attack from the reactor products.
Pretreatment valves
High-pressure separator letdown valves bring corrosive liquid containing entrained hydrogen gas to a much lower downstream pressure.
As the material passes through the valve, the gases exit the solution, creating a three-phase mixture that is extremely challenging for any control valve.
A good design should incorporate a multi-stage letdown with large flow passages to avoid clogging.
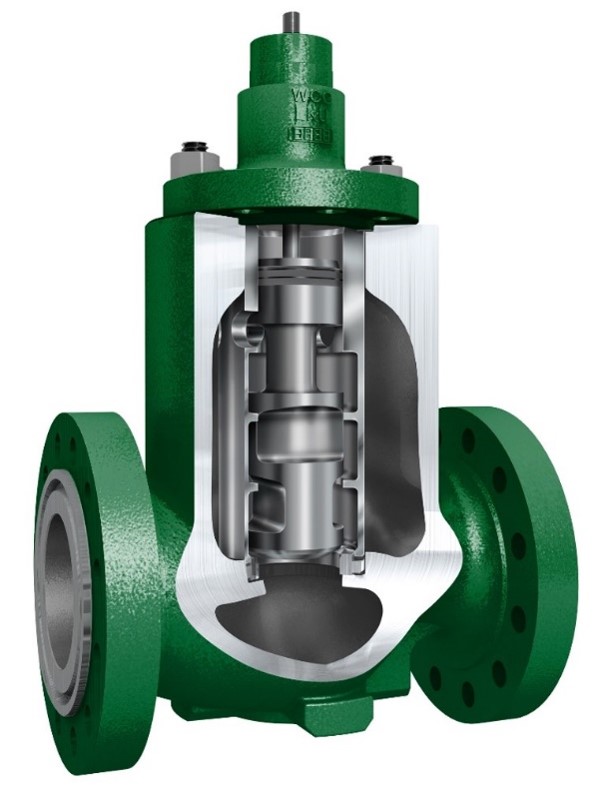
Separator letdown valves require multistage pressure drops, large flow passages, and high-strength alloys to handle the flashing, entrained particulates, and corrosion of this service. Valves such as the Fisher™ DST-G and Fisher™ NotchFlo DST can be good options.
Make an informed choice
As SAF production expands, keeping costs down will help refiners remain competitive. Choosing valves qualified to handle the unique challenges of SAF lipid conversion increases productivity and reduces costly maintenance outages. Consult with your valve vendor to learn more about the range of new technologies available for this application.
Visit the Separator Letdown Control Valve Solutions on Emerson.com for more on this technology and how it can help your operations withstand the harsh conditions and provide uninterrupted control.