Within the maintenance and reliability stream of the Emerson Exchange EMEA 2024 conference in Düsseldorf, Yazeed Otayf, control and instrumentation engineer at Saudi Aramco explained how they have optimized the control of pressure reducing stations to maximize the availability of these critical remote facilities.
Saudi Aramco has built a comprehensive oil and gas infrastructure in the Kingdom that ensures timely and efficient product delivery to its customers. The mission of its pipelines department is to maximize safety and efficiency of operations. Gas pressure reducing stations and valve stations are an integral part of the pipeline system. Redundant stations are used to reduce the pressure to pre-determined set points. The stations are remotely controlled from the operations coordination center (OCC) or locally through a supervisory computer.
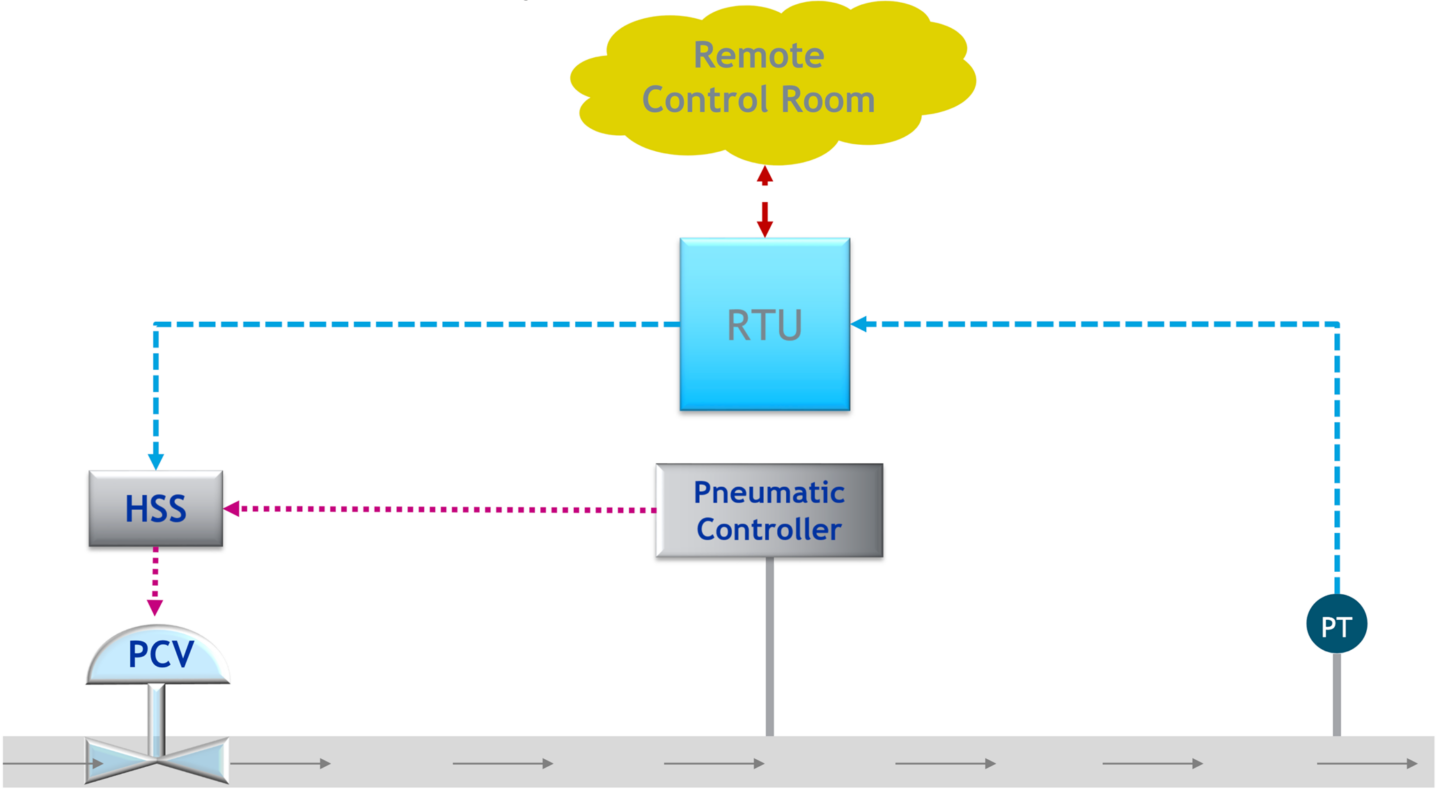
Pressure reducing station control scheme.
Otayf emphasized the importance of minimizing potential operational failures and interruptions. He explained that at the pressure reducing stations, redundant remote terminal units (RTUs) are installed in a master cabinet, which is connected to an expansion cabinet. One RTU rack and one expansion rack will always be online, with the remainder on standby. If the online rack fails, the standby rack will immediately take over.
Redundancy enhancements
Previously, the downstream pressure transmitters were connected to the expansion cabinet. Intermittently, the main RTU lost the readings from the downstream pressure transmitters due to a delay in communications between the main RTU and expansion cabinet. As a result, the master RTU changed the control mode from `Auto’ to `Manual’ instead of giving an undesired control output. As a result, the pneumatic controller took over and controlled the station. To resolve this, the physical connections from the pressure transmitters were changed from the expansion rack to the master RTU rack.
Another issue was that if there was a master RTU rack failure, the expansion rack would failover, reducing the availability of the system. To optimize the system availability, a delay was introduced to the expansion switching rack. To enhance operations, the analog inputs are validated by the RTU. Redundant downstream pressure transmitters are connected to the “master” RTU, with a 2oo3 voting system utilized, while redundant high side switches (HSS) are now connected to the pressure control valve.
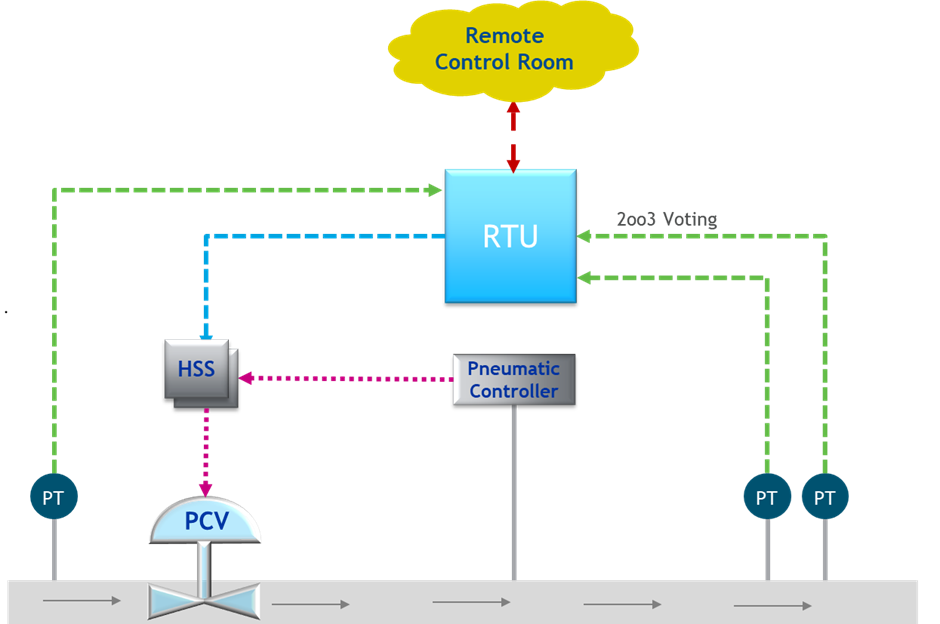
Control scheme redundancy optimization maximizes availability of the pressure reducing station.