Supercritical fluids are often found in carbon capture, ethylene, and hydrogen refining processes, and they pose unique equipment selection challenges, particularly for control valves. Our article on pages 45-50 in the February issue of Hydrocarbon Engineering, titled “Demystifying Control Valve Selection,” discusses key supercritical fluid applications, and it provides guidance for sizing and selecting control valves and trims.
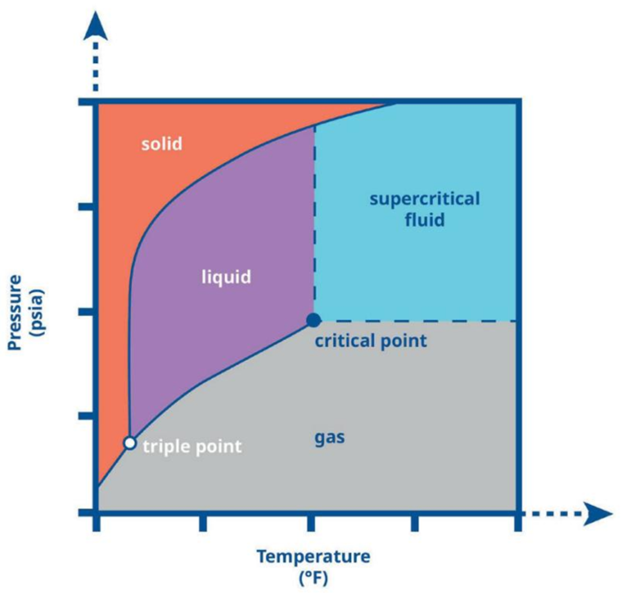
A fluid is in a supercritical state when it exceeds its critical pressure and temperature
Common applications
There are many reasons to put a substance in its supercritical state.
For example, carbon dioxide (CO2) in its supercritical fluid state is denser than its gaseous state, allowing for more throughput and/or lower velocities. Supercritical CO2 also has a lower viscosity than CO2 in a liquid state, resulting in lower line losses. In other cases, the altered solubility of a supercritical fluid is beneficial to the process.
Ethylene, CO2, hydrogen, and water are the four fluids most commonly used in their supercritical states.
Sizing concerns
Many valves are unknowingly installed in supercritical fluid processes. Some of these valves operate without issue, but others face frequent maintenance and flow capacity problems, best addressed with a more appropriately sized valve.
Traditional supercritical ethylene and CO2 applications are somewhat shielded from sizing-related problems because they experience relatively low pressure and pressure drops, but modern carbon capture and hydrogen production processes operate under higher pressures and are more vulnerable to sizing issues.
Accurate evaluation
Proper valve selection and sizing depend on both process conditions and the valve application. For example, an anti-surge valve and a vent valve installed downstream of a CO2 compressor may operate under similar conditions, but each plays a specific role with unique operating requirements.
The current IEC 60534-2-1 standard provides two control valve sizing models: one for incompressible fluids (liquids), and the other for compressible fluids (gases). Neither was designed to predict the required flow capacity for handling supercritical fluids.
In some cases, an approximation using one of these models may be sufficient, particularly if inlet conditions are close to supercritical boundaries. Deeper in the supercritical zone, the applicability of these models diminishes.
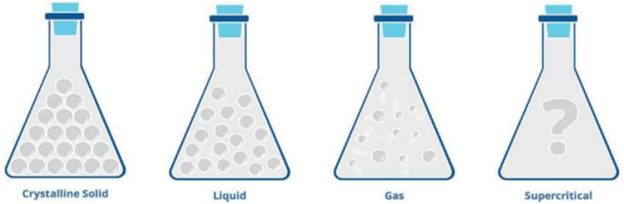
These beakers show molecular interaction in standard fluid states
The liquid model fails to account for supercritical fluid expansion, whereas the gas model may overestimate expansion. Either way, the valve may be improperly sized. In these cases, Emerson uses an internal methodology to evaluate the process media and more accurately calculate the required valve capacity.
In addition to the inlet and outlet, conditions must also be evaluated at the vena contracta, the area of lowest pressure within the valve, because the fluid may undergo a phase change or reach a temperature extreme at this point.
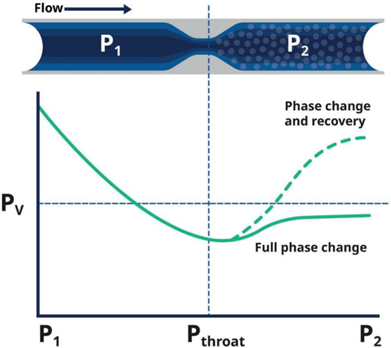
This diagram shows the pressure drop into a control valve throat with phase changes
Valve and trim selection
If the process fluid remains in a supercritical state at the inlet, outlet, and vena contracta, a standard trim will generally suffice. Conversely, a potential phase change at the vena contracta may require a specialized trim to avoid the change or mitigate damage. And finally, a phase change between the inlet and outlet requires further review to select the correct valve design and trim.
Because supercritical fluids fall outside the scope of typical IEC sizing, expert consultation is highly recommended to accurately predict phenomena, such as hydrodynamic and aerodynamic noise.
Key takeaways
Standard sizing methods are often inadequate for control valves in supercritical applications. A thorough evaluation of inlet, outlet, and vena contracta conditions, paired with advice from a control valve expert, will empower end users to make prudent valve sizing and selection decisions.