Going back to 1980s when I worked on offshore oil & gas production projects, it seemed that well test measurements could be a tricky business. Even with today’s technologies, the increase in unconventional oil & gas production continues to make well test measurements a challenge.
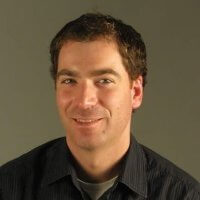
Michael Machuca
Upstream O&G Industry Marketing Manager
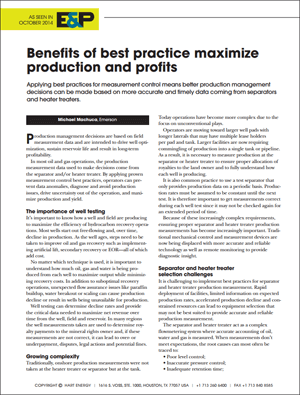
Michael highlights these unconventional oil & gas production challenges:
Operators are moving toward larger well pads with longer laterals that may have multiple lease holders per pad and tank. Larger facilities are now requiring commingling of production into a single tank or pipeline. As a result, it is necessary to measure production at the separator or heater treater to ensure proper allocation of royalties to the land owner and to fully understand how each well is producing.
Specifically, a separator and a heater treater are:
…a complex flowmetering system where accurate accounting of oil, water and gas is measured. When measurements don’t meet expectations, the root causes can most often be traced to:
- Poor level control;
- Inaccurate pressure control;
- Inadequate retention time;
- Poor temperature control;
- Flow control (valve sizing, stuck dump valves, etc.);
- Flow measurement errors;
- Operating error; and
- Poor well test management practices.
He offers some best practices to address these measurement challenges. I’ll highlight a few. Flowmeter diagnostics can assist in identifying gas carry-under, liquid carry-over, oil/water contamination and the health of the measurement device itself. Gas that separates out of the liquid through carry- under or entrained in the oil can lead to flow measurement inaccuracies and damage to the flowmeter.
In an earlier post, Understanding and Handling Entrained Gas Flow Measurement, we showed how some Coriolis flow measurement devices, such as Micro Motion ELITE Coriolis meters address these conditions. Michael describes these diagnostics:
…that uses the density and a measure of the energy consumed to keep the meter tubes vibrating called “drive gain” to detect entrained gas in the oil or water leg of the separator or heater treater. A drop in density associated with an increase in drive gain indicates free gas passing through the meter…
Similar diagnostic capability also can be used to detect liquid carry-over into the gas leg… In this case, it is an increase in density coupled with an increase in drive gain that indicates liquid carry-over.
A third diagnostic capability is realized when a density measurement that is higher or lower than expected on the oil or water leg, respectively, is used to identify oil/water contamination…
Pressure control is another area for best practice. If the pressure in a separator is too high:
…too many light components will stay in the liquid phase at the separator and will later release as gas in the tank, resulting in production loss due to venting or flaring. A high operating pressure also can increase backpressure on the well and decrease production.
To low, and:
…fewer intermediate hydrocarbon components will remain in the liquid, resulting in a decrease in the quality and volume of the produced crude oil.
It’s important to understand the variability of the flow rates to select the right pressure regulator to minimize well backpressure and optimize the oil, gas, and water separation process.
Michael closes:
Many operators are adopting technology such as Coriolis, ultrasonic, vortex and magnetic flowmeters for separator measurements. Each has advantages and disadvantages that should be evaluated based on the specific application requirements. Consultation with suppliers that offer a broad portfolio of measurement technologies will facilitate selecting the best meters that will provide diagnostic insights into how to improve separator and heater treater performance while minimizing total cost of ownership.
Implementing these separator and heater treater best practices will result in accurate and timely production data to enable reduced uncertainty in critical production management decisions and drive well optimization, reservoir life and long-term profitability.
Read the article for additional best practices. You can also connect and interact with other flow measurement, pressure regulator and oil and gas experts in the Flow, Regulators and Oil & Gas groups in the Emerson Exchange 365 community.
Update: The links to the article have been updated to a printable PDF version of the article.