This time of year, after our big Emerson Exchange conference, I like to go back and see what sessions I missed to be able to be able to recap for you.
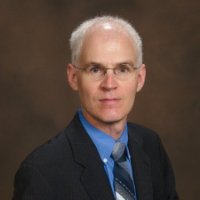
Mark Coughran
Process Control Consultant
They described several examples where control performance problems degraded oil & gas production operations or distracted operators. Mark and Gergo shared the methodology developed by the Control Performance consultants which they applied to examples presented.
The most common issue they see are loops put in manual mode because they oscillate when placed in automatic mode. Many sites, especially in remote locations, do not have personnel trained to diagnose and correct such problems. Mark highlighted the importance of isolating the problem to a particular component of the loop, preferably without going to the field for time-consuming (and possibly hazardous) examination and testing.
Some common issues causing these oscillatory conditions are PID loop tuning values, poor performance of the loop’s control valve and the control strategy applied.
Mark shared that the Control Performance team assists with services, tools, and training. The place to begin when addressing problems is with the measurement of the dynamic response of the process.
Next, as we highlighted in earlier posts, applying Lambda tuning in the controller gives non-oscillatory response within the response time required by the operations. For problems in other areas of the loop, additional expertise is often required.
One example they described was an offshore platform which had cascaded production separators in series—high-high pressure, high pressure, and low pressure. The level loops were cycling which caused disturbances downstream of the separators.
After performing the dynamic response measurements, the team working on this problem identified control valves in need of repair and applied lambda tuning to the level control loops. They also specified improvements in the control strategy to add robustness. The result of these actions was stabilized levels, flows and pressures.
The methodology the Control Performance consultants take is to first work with the producer or manufacturer to identify problems and opportunities to improve efficiency and reduce operator distraction. Next, the operations team is interviewed on items such as loop symptoms, process flow diagrams (PFDs), piping & instrument diagrams (P&IDs), and instrument reviews.
Out of these interviews a prioritized list and plan of execution is developed to perform the dynamic response tests with the Entech Toolkit or DeltaV InSight. If the response of the loop is not as it should be in manual mode, then the next step is to identify problems with the control valves, transmitters, process design, etc. After the problems are corrected the tests should be performed again.
Once the loop is operating correctly in manual mode, the controllers are tuned for non-oscillatory response with the required response time. With the loop now operating in automatic mode, if it is still not responding correctly, then it’s time to identify issues in the control strategy, logic, etc.
Once the loop is operating as it should in automatic mode, Mark noted that the setpoints can be moved closer to limits so that increases in production, reductions in energy usage, faster startups, reductions in operator distractions, etc. can be documented. These improvements are the basis for the return on investment (ROI) calculations that are performed to highlight the value of the control performance improvements.
This methodology can be repeated over time to keep the process operating at optimum performance levels. The Control Performance consultants can provide training to the local staff in the use of the methodology and tools or can perform these services at your facility.
You can also connect and interact with other process optimization professionals in the Operate & Maintain, DeltaV and Ovation groups in the Emerson Exchange 365 community.