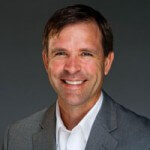
Douglas Morris
Power and Mining Industries Sr. Manager
The discussion about the impact of changing demographics has been around for a long time, but is it really taking place? I think this fact courtesy of the US Bureau of Labor Statistics (2010) says it all:
Half of the electric utility workforce will retire within the next ten years.
Both government and industry are trying to address this impending shortfall through education and development programs, but new employees simply don’t have the experience needed to make risk decisions. Plus, the industry’s workforce has steadily declined as utilities have not replaced skilled positions because of squeezed margins. I know firsthand that some companies which used to employ reliability specialists no longer have these departments…these companies will tell you they know the importance of reliability, but they just don’t have the resources anymore for a program. The impact on the industry is an ever increasing knowledge gap, but all is not lost as technologies and better design are helping to bridge this growing concern.
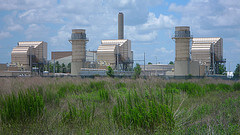
Source: Flickr, Daniel Oines (CC BY 2.0)
Another approach to augmenting your resources is to use outside expertise to help with both outage management and remote diagnoses of your plant. When your staff is small and doesn’t work on automation regularly, you don’t know all the tricks of the trade and outage work takes longer. You can offset this by utilizing automation experts to work onsite and perform automation maintenance services. You can also supplement your efforts with experienced industry experts who can help you diagnose performance and equipment problems remotely.
So the answer to the question is yes, the graying workforce is happening, but suppliers are working to help utilities bridge this demographic shift through easier to use equipment and supplemental expertise. Utilities looking for an approach to improve employee productivity and outage management now have some viable options.
To interact with other utility professionals, join us in the Power track of the Emerson Exchange 365 community.