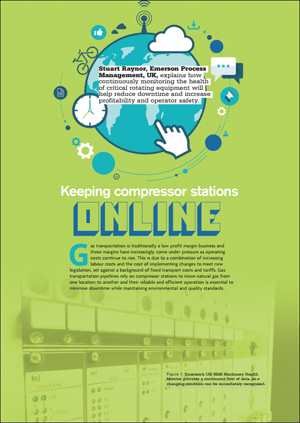
He describes compressor stations as being:
…used throughout the pipeline network [and] are based on centrifugal compressors drive by a gas turbine, or a reciprocating compressor driven by a piston gas engine (similar to an automobile engine).
Failures rarely happen without advanced warning:
Machinery health warning signs come in the form of vibration changes, process parameter changes and performance changes to name a few.
Online monitoring & analysis technologies include:
…temperature, vibration, efficiency and deviation data for changing conditions that could result in a shutdown.
Stuart describes the four components of a complete online monitoring solution for critical assets, such as these compressors:
- Shutdown protection monitoring (high vibration, axial position, overspeed).
- Prediction monitoring.
- Performance monitoring.
- Integration of all the above with the compressor station control system.
Shutdown protection monitoring functions:
…to prevent severe damage to the compressor or turbine, and more importantly injury or environmental hazard, in the event of a totally unpredictable event – for example, a turbine blade suddenly breaking away due to a metallurgical imperfection.
While these systems are mandatory for safety, when coupled with prediction monitoring, they can bring:
…’black box’ analysis after an unplanned emergency trip.
Prediction monitoring systems can help:
…identify potential faults and gauge their severity months in advance. This allows maintenance planners to determine the optimum time to make repairs, proactively order the right parts, and minimise their inventory operations.
Stuart noted one example, PeakVue, which we’ve highlighted in several earlier posts and helpful in monitoring real-time transient events associated with rolling element bearings and gearboxes, to name one example.
Online monitoring technologies such as the CSI 6500 Machinery Health Monitor continuously monitor to help spot deviations as they occur. By using this data, maintenance can be planned to avoid or minimize downtime.
Beyond temperature and vibration monitoring, a prediction monitoring system:
…also uses information gathered through oil analysis, infrared imaging, and ultrasonic detection.
Stuart described performance monitoring systems as:
…based on comparing the actual real-time performance of equipment, such as a reciprocating compressor, with design specifications… As equipment performance deteriorates, energy usage increases and throughput decreases.
Also, from a reliability standpoint:
…reductions in machinery thermal performance can be a precursor to mechanical health issues, and equally reduced machinery condition will inevitably affect the performance of that unit.
Stuart concluded the article:
Visibility to machinery condition and performance health before the protection system engages is considered the critical missing component in today’s machinery protection solutions. Operations and maintenance personnel are no longer looking for just protection capability when replacing an outdated protection system. They are requiring a complete and holistic protection, prediction and performance monitoring capability integrated with process automation.