A recent LinkedIn post, Leak Detection Market for Oil & Gas worth 2.71 Billion USD by 2020, at a CAGR of 7.1% highlights the purpose of these leak detection systems:
…to assist the pipeline operators and monitors in detecting and localizing the leakage. This leak detection system can detect the leakage at all stages of oil & gas industry such as upstream (exploration & production), midstream (pipeline networks), and downstream (refineries and storage tanks).
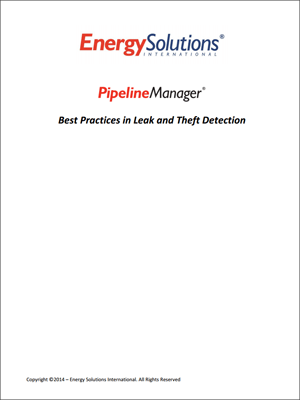
For a pipeline leak detection to be effective, it must be:
…able to detect leaks with limited false alarms. Too many false alarms and the system will be rendered practically useless. The system must also be able to cope with all operating conditions with minimal desensitization of the leak detection capability. Minimal desensitization is actually the difficult part.
The effectiveness of pipeline leak detection system (LDS) software is only as good as the measurement instrumentation feeding data to it.
Accurate, repeatable and available, correctly positioned instrumentation is required to maximize leak detection performance. It should then be accepted that any deficiencies in the instrumentation will ultimately lead to a reduced capability, whether in terms of minimum detectable leak size, accuracy of leak location, time to detect, number of false alarms or leak detection availability (a component of performance frequently overlooked).
Connecting this measurement instrumentation into data acquisition systems or control systems without losing accuracy is important:
If a measurement is specified to a given accuracy then the data acquisition must be able to transfer data to at least the same level of accuracy as provided by the instrumentation. For example, a pressure measurement accurate to 0.1% of a 100 bar range means that it is accurate to 0.1 bar. If a dead-band restriction is placed on the telemetry such that it only updates a value on exception greater than 0.5, or if the pressure readings are sampled from a location with 0.5 bar equipment induced noise then the pressure measurement value is instantly deteriorated to an accuracy of 0.5%.
The American Petroleum Institute’s API 1155 (replaced by API RP 1130) outlines requirements for leak detection systems
- Sensitivity: An LDS must ensure that the loss of fluid as a result of a leak is as small as possible. This places two requirements on the system: it must detect small leaks, and it must detect them quickly.
- Reliability: The user must be able to trust the LDS. This means that it must correctly report any real alarms, but it is equally important that it does not generate false alarms.
- Accuracy: Some LDS are able to calculate leak flow and leak location. This must be done accurately.
- Robustness: The LDS should continue to operate in non-ideal circumstances. For example, in case of a transducer failure, the system should detect the failure and continue to operate (possibly with necessary compromises such as reduced sensitivity).
Detecting leaks is done by comparing measurements at different locations along the pipeline looking for pressure measurement deviations (best for steady state single product liquid pipelines) and volume balance which determines the size of the leak (again for steady state flow in pipelines). Adding a real time model:
…attempts to replicate the physical hydraulic behaviour of the pipeline in real time, driven by flow, pressure, temperature and product property measurements obtained from the pipeline. It works by calculating detailed flow, pressure and temperature profiles at intermediate steps along the pipeline that are far smaller than the typical distances between line instruments.
A real time model:
…can significantly improve the accuracy of the two principal leak detection methodologies especially on systems with increasingly complex operation and behavior. The disadvantage of the real time model component is that more detailed information on the pipeline and equipment characteristics are required for its implementation, it can take longer to implement, it appears less robust and more complex to maintain… Graphical configuration and advancements in technology have helped significantly limit these disadvantages and perhaps surprisingly, the tuning times on site are not significantly increased in comparison to non-model based implementations.
Read the whitepaper for more on selecting the appropriate level of leak detection, system testing and how transient hydraulic real time model can under most operating conditions, with the right data input remove up to 99.9% of the process noise from any signal, and thereby detect very small leaks.
You can also connect and interact with other pipeline experts in the Oil & Gas group in the Emerson Exchange 365 community.