Marcelo Dultra, Process Industry Director at Emerson, recently published the Cover Story for the June 2021 issue of Valve World. The Cover Story describes how digital technology is being applied to pressure relief valves to reduce emissions, monitor performance, and save money. It’s titled PRV Digital Transformation Byte-by-Byte and is summarized below.
Pressure relief valves (PRVs) are safe, reliable, and decidedly non-digital. Their function is critical, often serving as the last line of defense to avoid catastrophic process overpressure, so they rely on simple and proven mechanical mechanisms to achieve their purpose. These designs have remained largely unchanged for over a century.
Their lack of electronics or external controls makes PRVs very robust, but also makes them difficult to monitor (Figure 1). A PRV can simmer, continuously leaking product or hazardous gases, and the plant has no way of detecting the condition. Fortunately, recently introduced instrumentation addresses this and other issues, making PRVs low-hanging fruit for digital transformation.
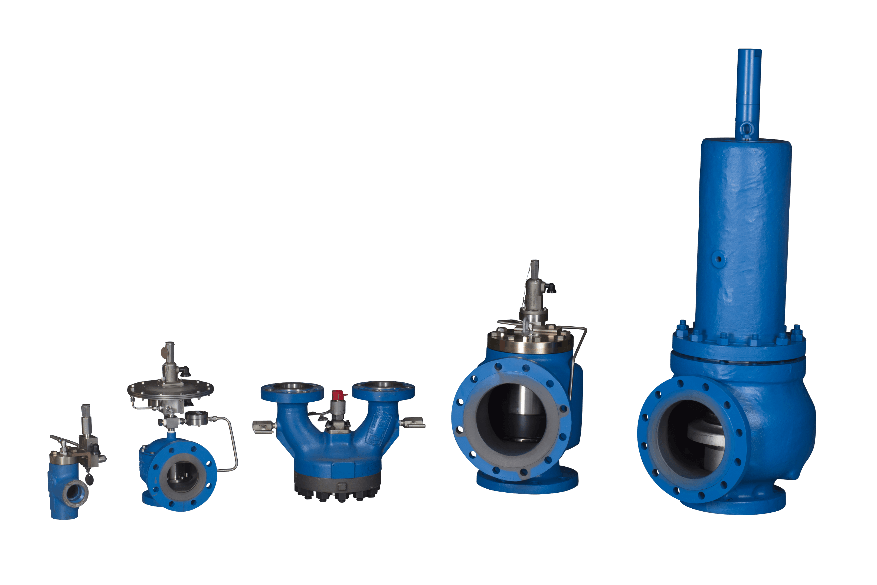
PRVs are typically not connected to control and monitoring systems, presenting problems for process plant operations.
Old and new challenges
In a perfect world, a PRV should never operate at all. In fact, it is not uncommon for a PRV to go years between overpressure events. However when called to action, a PRV must lift and mitigate the overpressure condition, then seat fully to avoid leakage. It is that last part that is particularly difficult.
Depending on the process scenario, the PRV may chatter as it relieves, slamming the seat repeatedly until the pressure has been vented. Or the PRV may simmer, opening and closing slightly when the process pressure is hovering near the PRV setpoint. In either case, the seat often gets damaged and the valve starts to leak.
Detecting those leaks can be quite challenging for a number of reasons. First the PRVs are often located at the tops of columns, boilers, and other process vessels. This is an excellent location to vent vapor, but it is also very inaccessible. PRVs often direct their discharges into vent headers or flare headers, making the PRV status difficult to detect. A valve can leak and vent for hours or even days, and never be noticed.
However, tightening environmental regulations are forcing industry to curb these emissions, so companies must send operators to the highest reaches of their plant to monitor for leaks. Unfortunately, long term leaks still go undetected, wasting valuable product or venting hazardous chemicals into the atmosphere. Marcelo describes the magnitude of the problem:
A single valve with a leakage rate of 0.1 percent of the rated capacity will annualize a volumetric release equivalent to a valve fully open for six hours. Based on Emerson’s research, a typical 250,000 BPD refinery could be wasting over USD $1.5m per year in product and energy losses.
Releases and leakages (see chart below) can lead to fines, lawsuits, and extra work related to identifying the source and the reporting of each release. Even small leaks can generate large amounts of VOCs, depending on concentration and pressures.
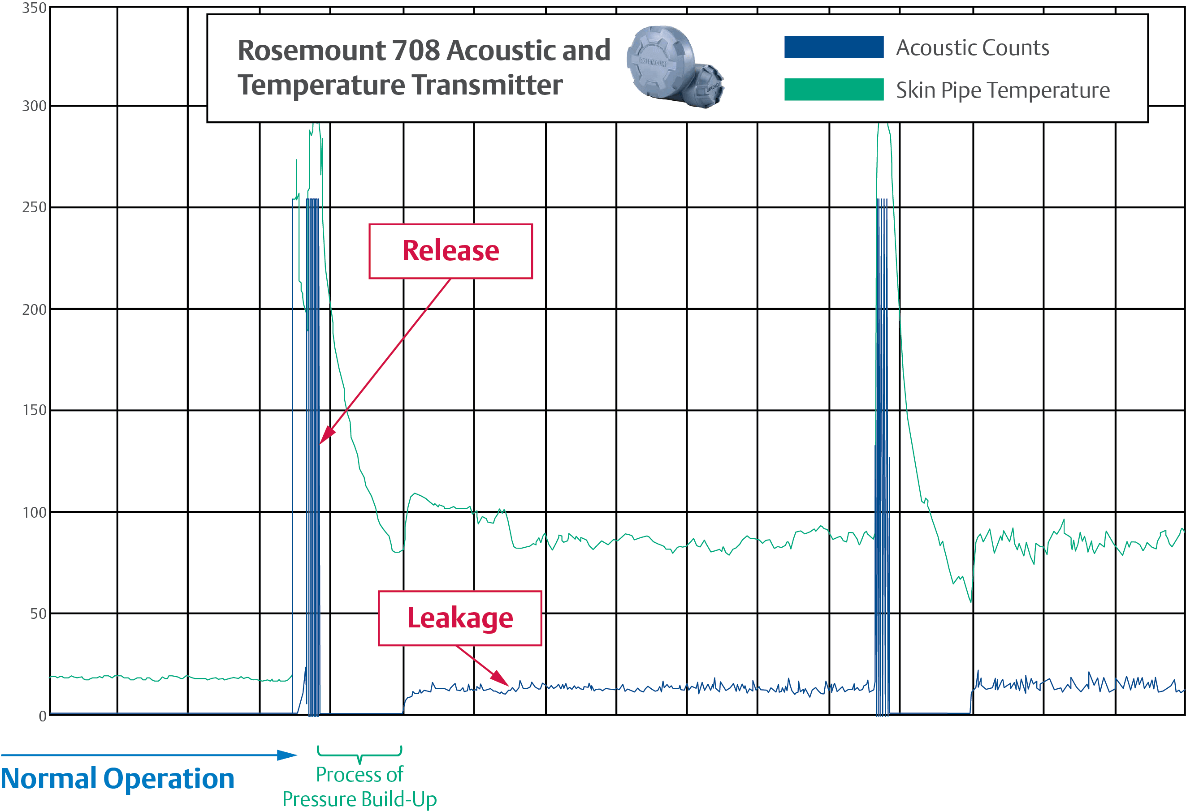
This graph illustrates a typical leakage event. After the first blow down, the valve does not shut completely. Leakage, shown by the blue line, persists but is detected by an increase in skin temperature, shown by the green line.
Plants have traditionally tried to minimize the leak problem by periodically pulling and overhauling their relief valves. ASME Section 1 code requires boiler PRVs to be pulled on an annual basis, but even process relief valves are often serviced every three years or less. This does help ensure the relief valves will open when required—but it requires a great deal of time, effort, and expense—and it does little to minimize leaks. If a PRV lifts a week after being returned to service, it might leak for years until it is serviced again. Such leaks do occur, as Marcelo mentions:
When valves arrive for service, they undergo a pretest process where the set pressure is applied to the valve to make sure it will open on demand. Analysis showed 20 percent of the valves leaked during pretest at less than 50 percent of set pressure, and 8 percent of the valves leaked so much that the testing system did not have enough capacity to open the valves.
Fortunately, advances in wireless technology have created solutions to this problem.
PRVs Go Digital
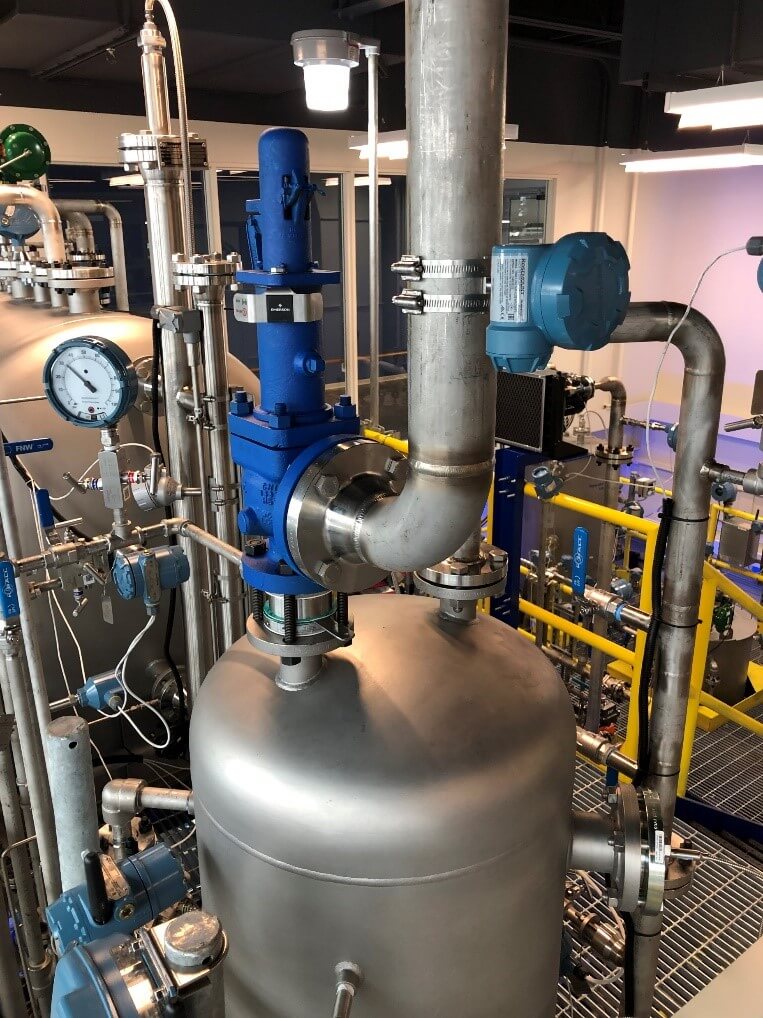
An acoustic transmitter (blue device in the upper left of the photo), can be mounted on the discharge pipe of a PRV, allowing it to detect the vibrations caused by any release. These devices send data via WirelessHART.
Recently introduced acoustic monitors with wireless communications can now be mounted on the discharge piping of critical PRVs (see right
side photo). Alternately, wireless skin temperature transmitters can be installed. In either case, the new transmitters are able to detect when a PRV relieves and if it is leaking.
Such technology allows a PRV to be monitored in real time, indicating when a PRV lifts, how long it releases, and if it fails to seat completely. Such information is critical to plant operations for a number of reasons. PRV release events can be immediately detected and hopefully avoided in the future. If a PRV does vent, the length of the release is often required information for environmental regulations. Finally leaking PRVs can be immediately identified and repaired.
Real World Savings
Recent projects utilizing these technologies have generated significant cost reductions. Marcelo describes two such projects below:
To improve its flare system management and comply with EPA-rules, a U.S. refinery installed 69 PRV WirelessHART monitors. After 15 months, the system detected over 200 release events, each with potential high flow rates and H2S emissions. They identified 20 problematic valves, including three valves where the bypasses were found open. The project paid for itself within five months with reductions in hydrocarbon losses, and increased throughput and revenue.
One of the world’s largest refineries in Asia saved USD$500,000 in one year in lost hydrogen by detecting leaking vent valves and PRVs, along with USD$200,000 per year in saved hydrocarbon losses.
Conclusion
Digital transformation may seem like an intimidating undertaking, but in the case of PRV monitoring, benefits are significant and relatively easy to achieve. If your facility is battling these types of issues, a bolt-on technical solution is close at hand.
Visit the Pressure Relief Valve Wireless Monitoring section on Emerson.com for more on the advantages of digitalization of your pressure relief valves. You can also connect and interact with pressure relief valve experts in the Valves, Actuators & Regulators group in the Emerson Exchange 365 community.