Pharmaceutical and biotech manufacturing processes are complex and require well integrated and documented flows of information from upfront forecast demand and customer orders through the production process to inventory receipt and order fulfillment. The components from the enterprise resource planning (ERP) software to the measurement, final control elements, and control systems on the production floor need to support this information flow—or a lot of manual effort is required to bridge the gaps.
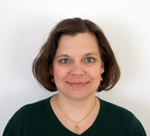
Michalle Adkins
Manager, Life Sciences Consulting
An important concern she hears is that operators want a consistent mechanisms for production process visibility; process engineers want to be able to readily retrieve data for comparing batches and providing necessary information for deviation investigations, and quality personnel want to be able to quickly understand deviations to determine batch quality implications. In addition the integration of key pieces of data, whether manual, programmable logic controller (PLC), or distributed control system (DCS) controlled need to work consistently as integrated to the ERP system.
The functions performed by the ERP include forecast, raw material requirements & purchasing, inventory receipts & management, and manufacturing order schedule. This flow of activity feeds the Current Good Manufacturing Practices (cGMPs) critical zone which includes component weigh & dispense operations and the manufacturing process execution. This execution integrates manufacturing records, standard operating procedures, equipment records, and the training records of individuals involved in the execution process.
The information collected during this execution zone of activity feeds the quality control (QC) review and release process that also relies on the online and offline analytical testing. During this whole process, the information flows back to the ERP where order receipt and fulfillment processes are performed.
Performing the formulation in control systems such as the DeltaV distributed control system and integrating any high-speed fill/finish operations managed by PLCs provide common operator displays and decreased commissioning times. Diagnostics from smart instrumentation eliminates unnecessary problem solving trips to the field.
Having common operating displays for the manual, PLC-based, and DeltaV-based areas of control leads to fewer deviations since operators operate through a common window into the process. Fewer deviations means less discarded and expired batches, reduced inventory on hold, and reduced inventory carrying costs. Change control is also simplified with the batch running in the DeltaV system. In cases where PLCs perform very high-speed control, the batch logic directs the PLCs to perform the necessary steps.
Beyond operator displays, consolidating batch and process control data improves overall process visibility and reduces deviation investigation resolution times since all the pertinent data is available in one system. With manufacturing execution systems, such as Syncade suite, operating above the control system, the rest of the GMP critical zone activities and the associated data can be readily assembled into an electronic batch record while managing the integration of data to the ERP system.
Michalle noted that Emerson has successfully implemented parenteral fill finish with a DeltaV system in formulation and the DeltaV system integrated with PLCs in the parenteral fill/finish facility as well as DeltaV with Syncade integrated with PLCs in a parenteral fill/finish facillity.
To connect and interact with Michalle and the Life Sciences consultant team, join the Life Sciences track in the Emerson Exchange 365 community.