For many process manufacturers with lean engineering staffs, partnering with outside automation specialists is critical for successful automation and optimization projects.
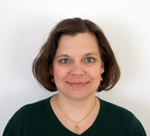
Michalle Adkins
Manager, Life Sciences Consulting
The project execution lifecycle typically contains five phases:
- Project Assessment & Planning—Consulting Study
- Front End Engineering Design (FEED)
- Detailed Design, Implementation, and Testing
- Onsite Deployment
- Support & Maintenance
The team mainly works with clients in the first two phases. In the project assessment & planning phase, success typically requires the following activities:
- Develop Executive Sponsorship
- Finalize Business Objectives
- Finalize Business Case
- Develop User Requirements Specifications
- Create High Level Scope Definition
- Develop High Level Implementation Strategy
- Create Resource Strategy
- Prepare Budget and Schedule Estimates
In addition, this is an effective mechanism for evaluating scenarios and meeting requirements for critical phases of the project while understanding and preparing for the business and organizational impacts.
Defining requirements based on the business challenges and goals leads to a clearer understanding of the potential investment and return on that investment. The greatest influence on the direction of a project occurs earliest in the project. As the project advances costs to make changes increase, especially as the end of the project nears.
Michalle shared her team’s general methodology to a study. First, it is important to establish an interview schedule and define the preliminary data requirements. Next, site interviews are scheduled and performed to gather data and assess current state of the operations as well as to evaluate the business processes.
The next step is to define the future state options and their associated processes. With these options, the team can define scope and phases to attain the future state. Analyzing options helps to clarify which path to take.
With the path identified, it’s time to roll out the planning and work through project road maps, design decisions, deployment, and risk mitigation. This planning helps to form the high-level project execution strategy. The final portion of the methodology is to think through the organizational change that will be required and work through how to manage this change.
Deliverables from this process include value stream maps, a financial analysis of the project’s impact on the business, a user requirement specification, final report, and a basis of design (BOD). This BOD’s overview includes the goals, scope, methodology, vision, and a high-level view of the current state, future state, and project scope discussions. It also includes details by business processes—materials, batch records, weigh & dispense operations, etc. The final part of the BOD describes how the project execution plan should unfold.
As we highlighted in an earlier post, Prototyping Key in Manufacturing Execution System Projects, Michalle strongly recommends prototyping be performed to align visions and explore the organizational and culture changes that may be required.
She sums up the critical success factors:
- Early and continued engagement of the operations and training staff
- Make Key decisions early – Finalize vision and requirements early and document them
- Dedicated “Power Users” to learn the application and train the remainder of the operations staff
- Effective handover from Implementation team to site support
- Extremely supportive business leadership and staff (Quality Assurance [QA]/Tech Service/Operations/IT) – Operations driven
- Balance perfecting software against getting to done.
If you’d like to connect and interact with Michalle and the Life Science Consulting team as well as other pharmaceutical and biotech professionals, join the Life Sciences track of the Emerson Exchange 365 community.